モノづくりの中小メーカーが、ISO9000を導入する際にあるべき姿の設計・開発のルールを作ってしまうと、
- 大メーカーや自動車業界のような設計・開発プロセスとなる。
- 目的の分からないDRのために書類を準備する工数が増える。
- 設計者は設計以外の仕事(書類の準備)に時間を取られ、設計の時間が減ってしまう。
- 結果、品質・コスト・納期は以前と変わらない。
といった状況になってしまいます。
自社に合わせた設計・開発プロセスとなっていないことが問題なのですが、だからといってどうすればよいのか悩んでいるモノづくりメーカーも少なくないのではないでしょうか。
ここでは、もう少し具体的にモノづくりメーカーによる設計・開発プロセスの現実(推測も含みます)について見直し、設計スピードを上げる「設計の再開発」についてまとめています。
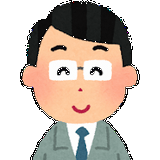
会社規模が小さくても高品質の製品を供給している例もありますが、部品、組部品、製品で分けた方が分かりやすいと考えたため、会社規模の違う3つの会社を想定して説明します。
ISO9000(品質マネジメント)が求める設計・開発プロセスについては、以下にまとめまています。
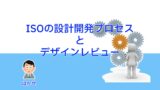
想定しているモノづくりメーカーについて
ここでは、具体的に検討するために、下表の会社を想定します。
会社の分類 | 製造しているモノ |
---|---|
A社(大企業) |
|
B社(中小企業) |
|
C社(零細企業、町工場) |
|
モノの流れで説明すると、
C社の部品 --> B社の組部品 --> A社の製品
組部品や部品は複数の会社から購入するため会社の数は、
C社 >>> B社 >> A社
となります。
会社規模による設計・開発フローの比較
早速ですが、A社(大企業)、B社(中小企業)、C社(零細企業、町工場)でありがちな設計・開発フローを下図に示します。
DR(デザインレビュー)の部分をあえて色分けしています。
図1 会社規模による設計・開発フローの例
会社規模により、設計・開発フローに違いがあって当然なのですが、ISO9000を取っているのに設計品質が改善されないなどの悩みを持つ会社においては、図1の大企業の設計・開発プロセスを(多少は自社に合わせアレンジはしていますが)そのまま品質マニュアルや設計・開発規定に定めていることが多のではないでしょうか。
なぜ、大企業の設計・開発プロセスをほぼそのまま設計・開発規定としてしまうのでしょうか?
自社の設計・開発プロセスに、大企業の設計・開発プロセスを当てはめてしまう理由の1つは、そもそも自社の設計・開発プロセス自体が不明確であり、社内ルールというよりは暗黙知に近い形で設計・開発を進めていたのではないかと考えています。
これは、ISO9000を導入した際に大企業のサンプルを真似て形だけ導入してしまった場合にも、ISOの形骸化として次の様な問題になってしまいます。
- 設計・開発に関する書式がやたらと多くDRの準備が大変だ。
- 書類さえ準備できていればDRは何とかなるという運用になっている。
- 設計・開発の1つ1つの書類(書式)の内容が難しい。
- 書類の意味はよく分からないが、とにかく空欄をなくすことに注力している。
- DRのためのDRになっている。手段としてのDRなのに、DRをすることが目的となっている。
最も大企業の場合であっても、図1のフロー通り実施しているかどうかはよく分かりませんし、販売後に製品不具合が発覚したり、モノづくりのメーカーの代表例である自動車においてもリコールが少なくない現実からは、DRをやっていれば品質不具合が発生しないということではないと考えています。
製造物責任法(PL法)によるメーカー(製造業者等)の損害賠償責任対策の影響もあるとは思いますが、3D CADやCAEによるシミュレーションが使われている設計の場において、何か起きているのではないかと感じています。
それでは、図1を使い会社規模による設計・開発フローについて詳しくみていきます。
なお、図1のDRは、いわゆるデザインレビュー(設計審査)だけでなく、各プロセスについてのレビューという広い意味で使っています。
この際の判断基準となる主な要素には次のようなものがあります。
要素 | 補足説明 |
---|---|
品質(Quality) |
|
コスト(Cost) |
|
納期(Delivery date) |
|
特許(Patent) |
|
大企業(製品)
製品を販売するメーカーです。
DRの数を数えてみると、
- 商品企画では、1回
- 設計では、構想、基本と詳細設計で計3回
- 試作では、試作と量産移行で計2回
商品企画から量産移行まで合計6回のDRがあります。
例えば、1台の自動車の総部品数が2~3万点とも言われる自動車であれば、それぞれの段階で行われ場計6回(実際にはもっと多いのかもしれません)のDRが必要であり、実施されているのかもしれません。
製品開発のトータルコストを下げるための手段の1つとして、CAEによるシミュレーションを活用して、設計・開発に必要なリソースを製品開発の前段の割合を増やすことも行われていますが、製品出荷後にリコールが繰り返されているところに設計の問題が隠れているように感じています。
中小企業(組部品)
大手メーカーから組部品を受注して生産する中小企業では、ISO9001:2015の認証取得を維持していても、以下の理由により適用除外を受けているケースもあるようです。
- 製品の設計は、大手メーカーが行っている。
- 自社で設計していない。
- 生産は、大手メーカーの指示通り行っている。
- 自社で作業手順や工程設計をしていない。
ここでは、組部品を製造できる規模の中小企業における製品開発について、図1を例に考えてみます。
社員数でいくと20名規模を想定していますが、この規模になると、商品規格、設計、試作、量産などのプロセスこそあれ、担当者をみると兼務が多くなります。
技術的に詳しい人(ベテラン)になると、設計で1人、製造に1人といったところです。
図1の例では、商品企画(製品のアイディア)が出ると、設計のベテランが設計仕様を検討し、即詳細設計を始めます。
詳細設計のアウトプットとしての図面ができると、今度は製造のベテランが試作品を作り、この試作品でDRを行い量産が開始されます。
設計の部分、大企業が構想、基本、詳細と設計を進めていたものを、設計仕様「仕様書」と詳細設計「図面」で済ませてしまう。
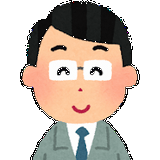
設計のベテランや製造のベテランは、個人の力量としてみれば、これはこれで優秀ということになるのかもしれませんが、典型的な属人化の例でもあり会社としてみるとリスクしかないと考えています。
設計と製造のベテラン任せと言えば聞こえはよさそうですが、量産開始後はそれこそ出たとこ勝負となります。
クレームに限らず量産での不具合などを含め、何事か起こるとベテラン意外にはどうすることもできません。時にはベテランでさえ手に負えないケースもあります。
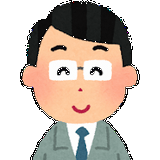
ベテランも人間です。
人間であればヒューマンエラー(人為的ミス)はあります。
「人はミスをする」ことを受け入れないとモノづくりは良くならないと考えています。
こうなるとどうにもなりません。何とかしなければならないので、何とかすることになるのですが、最終的には「お茶を濁して蓋をする」結果となります。
ベテランの高齢化に対応したくとも、
- ベテランは、属人化したノウハウ(ISO9000でいう組織の知識)を伝えることが苦手
- ノウハウを受け取る側の力量も不足
何とかしろと社長が指示したとしても、
- 最後までノウハウはベテランの頭の中
ということが多いように思います。
町工場(部品)
ここでの町工場とは、中小企業から部品(単体)の注文を受けて作る小さな工場のことです。
社員数を多くて数名、ISO9000の認証取得をしていない会社がほとんどではないかと思います。
この規模になると、中小企業から提供された仕様書と図面からいきなり量産となります。
判断が必要なことは、工場長、もしくは社長自らということも少なくありません。
加工が難しいような部品や初めて作る部品は、サンプル品を作ることもありますが、同じ中小企業からの注文をある程度受けていると、サンプル品なしで量産ということもあるようです。
当然、設計はしていないので、加工費用で利益を出すような経営になります。
品質、コスト、納期そして利益について考える
モノづくりにおける品質、コスト、納期については、
- 品質は当たり前
- 納期を守るのも当たり前
- 残りのコストは下げ方向のみ
というのが現状かと思います。
これまで説明してきた大企業(製品)、中小企業(組部品)、町工場(部品)のメーカーとしての利益について振り返ってみます。
大企業は製品を販売しますので、原価に販管費や利益を含めて販売し、会社として利益を得ます。
中小企業は組部品を販売しますので、加工費、組み立て費、設計や工程設計などを含めた代金を発注元の大企業から得ます。また、自社設計品であれば、組部品単体での販売利益を上げることもできます。
町工場は何を売っているか、設計も製造も発注元の中小企業の指示通り、材料も支給されてしまうと、加工費しか利益になりません。
モノとしての製品の利益配分について考えてみます。
製品を販売することでお客様から代金を得ます。この代金から、大企業は利益を得ることができます。
中小企業も組部品として大企業から代金を得られるので、大企業が受け取った製品代金の中の利益の一部を得られると考えてもよさそうです。
しかし、町工場となると、部品の加工賃は部品代金に含まれてしまうので、製品代金の中の利益の一部は得られそうにありません。
これは、なかなか厳しい現実でもあります。モノづくりは日本のお家芸と言われることもありますが、それは、町工場のような零細企業の利益が製品価格に含まれていないことによるコストダウンの結果とも考えることができるのではないでしょうか。
製品の付加価値が、製品に付加された価値ではなく、製品を作るために必要な加工費用を削った結果であるとしたら、モノづくりの設計部分での付加価値ではなく、生産部分でのコストダウンによる付加価値だけで勝負していることになります。
製品の製造コストは、設計でほぼ決まります。この部分でのコストダウンや設計品質を高める設計に、日本のモノづくりが輝きを失っているように見える原因が隠れているように感じています。
これまで述べてきたことは、私個人の考えではありますが、モノづくりの中小企業に対する新しい取り組みを行っている会社の1つにキャディ株式会社があります。
キャディ株式会社の代表取締役 加藤氏の代表挨拶から以下、引用させていただきます。
キャディ株式会社が生まれてくるような今の時代、私がこれまで述べてきたことも極論ではないのだと考えています。
かつて、「Japan as no.1」と言われた日本のモノづくりは、いつの間にか「斜陽産業」のような形で報道される機会が多くなりました。国内の中小メーカーは、30年で半数以上が廃業し、現在もメーカーの73%が赤字に苦しんでいるという厳しい現実があるのも事実です。
「モノづくり産業のポテンシャルを解放する」
我々が掲げる企業理念(ミッション)です。高品質な製品をリーズナブルな価格で安定供給する体制で、お客様の安定調達に貢献する。得意領域に特化して安定的に受発注できる仕組みで、加工会社様の安定利益体質化に寄与する。まずは、板金加工や金属加工・切削加工の分野でこれを実現していく所存です。
キャディ株式会社 代表メッセージより(2020年3月24日現在)
短納期を実現する設計スピード
ここで、お客様の要求する製品を供給するためのモノづくりについて、白紙的に考えてみます。
- 受注では、これまでの受注実績や失敗を振り返ることにより、当社理由による返品などは防げそうです。
- 多くない利益をさらに圧迫するのが手戻りです。中でも設計起因の手戻りによる原価(設計者の工数)は把握しにくいこともあり、隠れた利益削減要因となっていることは間違いなさそうです。
- 製造については、上述のC社は加工賃だけですし、おそらくこれ以上のコストカットが難しいレベルなので、設計が変わらないとさらなるコストダウンは難しそうです。
それでは、モノづくりにおける品質、コスト、納期について何に取り組めばよいのか改めて考えてみると、
- 品質は当たり前(変わらない)
- 納期を守るのも当たり前(設計プロセスの短縮)
- コスト(手戻りをなくす設計、製造コストを下げる設計)
どうやら次の様なイメージの設計の改善「設計の再開発」に取り組むことで、モノづくりメーカーとしての競争力を上げることができそうだと考えています。
- 品質はこれまで通り落とすことなく(コスト削減につながる設計変更は進めて)
- 設計スピードを上げることで顧客要求から製造までの期間を短くし
- 設計の質を上げることで手戻りを減らす(手戻りのない設計ができるように)
中小企業や町工場では、経営者や社員(設計や製造のベテラン)の高齢化が進み、黒字での廃業も珍しいことではなくなり、中小企業を買いたい、売りたいというニーズから中小企業の売買環境も整ってきています。
何かできることはないものかと考えてはいますが、妙案があるわけではありません。
3D CADというシミュレーションもできる設計ツールの出現し、モノづくりに必須となっている今、もはやコスト削減の限界にきてしまっている製造分野ではなく、ツールが新しく協力になった設計分野で品質、コスト、納期(設計スピード)を改善する手段として、「設計の再開発」ができないものかと考えています。
まとめ
モノづくりメーカーの中小企業が、ISO導入の際あるべき姿の設計・開発のルールを作ってしまうと、大メーカーや自動車業界のような設計・開発プロセスとなり、目的の分からないDRのための書類を準備したりして、設計者は設計以外の仕事に時間を取られることになり、結果、品質・コスト・納期は以前と変わらずといった状況になってしまいます。
ここでは、会社規模による設計・開発フローを比較し、品質・コスト・納期について振り返り、短納期を実現する設計スピードについて、以下の項目で説明します。
- 想定しているモノづくりメーカーについて
- 会社規模による設計・開発フローの比較
- 大企業(製品)
- 中小企業(組部品)
- 町工場(部品)
- 品質、コスト、納期そして利益について考える
- 短納期を実現する設計スピード