3Sといえば、「整理・整頓・清掃の3S」ですが、「モノづくりでやってはいけない3S」があります。
工場などのモノづくりの現場での問題や課題に気づくだけでなく、経営上も重要なキーワードでもあります
「モノづくりでやってはいけない3S」とは、次の3つです。
- 先送り(Sakiokuri)
- 仕損(Shison)
- 仕掛り(Shikakari)
ここでは、中小企業のモノづくりメーカーを想定して、モノづくりで「やってはいけない3S」について説明します。
先送り(問題の対策の先送り)
先送りとは、問題に気づいても対策せず、先送りすることです。
モノづくりの現場では、好むと好まざるとを問わず、毎日大小様々な問題が発生しています。
例えば、生産計画1つとっても変更があることが当たり前であり、変更が前提の様になっているのではないでしょうか?
せっかく問題に気づいても、「今は忙しい」、「次の仕事がある」など理由は様々あるのでしょうが、次の様な先送りをすることは、問題を放置させておくことになってしまいます。
- 問題が発生しても、再発しても次に起きたら検討しようと先送り
- せっかく対策を決めても、これまでとやり方が変わるからと先送り
やがて、問題や対策を先送りすることは、問題を放置しているのと変わらないため、
- 問題そのものや対策が大きくなっていく
- 問題解決に必要な時間が長くなっていく
など、マイナスの影響が増えていくことになります。
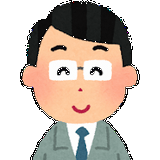
職場でも、もしかすると、個人的にも思い当たることがあるかもしれません。
現場でのモノづくりで発生した問題については、製品の品質を維持するためにも、三現主義で、
- 現場で
- 現物をみながら
- 現実的に検討する
ことが重要です。
現場重視の考え方である三現主義と5ゲン主義については、以下をご参照ください。
仕損(工程不良品)
仕損(しそん)とは、モノづくりの現場で発生する、工程不良品のことです。
例えば、自社生産の場合に工程不良品が発生すると、
- 不良品に使った材料が無駄になります。
- 不良品を作った時間(工数)が無駄になります。
- 納期までのリードタイムが短く、あるいは、なくなります。
- 割り込みの生産をすれば通常の生産よりコストが増えます。
さらに、
- 不良品の製造ロットを再検査する時間が必要になります。
- 不良品を生産した分だけ、製品原価が上がります。
- 不良品を生産した工程の生産効率は落ちます。
- 不良品を生産した分の稼働時間が無駄になります。
購入品の場合には、購入した不良部品を製品に組み込んでしまった不良発生に気づかず社外に流出させてしまうと、次の様にコストだけでなく会社や製品のブランドイメージにもマイナスの影響となります。
- 社外では、代替品の発送、回収費用、不良品を販売したというマイナスのイメージなどにつながります。
- 社内では、製品の生産中断、不良部品を組み込んだロットの調査、手直しや作り直しなど工数もコストもかかることばかりです。
仕損が発生しないようにするためには、
- 自社の工程品質の作りこみ(安定して良品を生産できる)
- 購入品の部材メーカーへの品質管理
が重要です。
仕損の発生を防ぐための方法の1つに、三ム(ムリ、ムダ、ムラ)に注目する方法があります。
- ムリ(無理):ムリな作業、ムリな置き場など
- ムダ(無駄):ムダな動き、ムダな仕掛品など
- ムラ(むら):ムラのある動き、ムラのある教育など
仕損、不良品が発生した原因を調べることで、再発を防ぐ対策を現場、現実に合わせて進めていくことが重要です。
仕掛り(つくりかけの製品)
仕掛りは、工程途中のつくりかけの製品のことです。
仕掛りが発生する例(工程)には、次のような理由により工程内の作業を進められない場合があります。
- 工程内で必要な部品がない。
- 必要な加工をする設備が使えない(設備の消耗品の損耗、設備の故障)。
- 加工途中で割り込みの作業が入り中断した。
また、次のように仕掛りの発生している工程の前後の工程に問題がある場合もあります。
- 前工程から送られてくる数量の変動が大きく、結果的に仕掛りが増える。
- 後工程での加工数量の変動が大きく、仕掛り品を準備しておく必要がある。
つまり、前後の工程を含めた生産バランス(生産速度)が取れていないため、仕方なく自工程で必要以上の仕掛り品を保管(在庫)している場合です。
このような場合、保管場所の問題だけでなく、次の様な問題も発生している場合があるので注意が必要です。
- ボトルネックとなっている工程ではフル生産していれ、工程に余裕がない。
- 緊急生産が毎日発生するなど常態化している。
各工程の生産バランスを改善するためには、次のような取り組みがあります。
- 仕掛り品の多い工程と関連する工程の生産を全体的に再調整する。
- 仕掛り品を減らせない場合には、仕掛り品の識別管理や置場の管理を見直してムダを減らす。
また、営業と製造との調整になりますが、次の様なことも行います。
- お客様の発注情報(数量や納期)の調整を事前に行い、無理な生産計画にならないようにする。
- 生産計画変更に関する情報についての関係者との連携
まとめ
3Sといえば、「整理・整頓・清掃の3S」ですが、「モノづくりでやってはいけない3S」があります。
「モノづくりでやってはいけない3S」とは、先送り(Sakiokuri)、仕損(Shison)、仕掛り(Shikakari)の3つのことで、工場などのモノづくりの現場での問題や課題に気づくだけでなく、経営上も重要なキーワードでもあります。
ここでは、中小企業のモノづくりメーカーを想定して、モノづくりでやってはいけない3Sについて以下の項目で説明しました。
- 先送り(問題の対策の先送り)
- 仕損(工程不良品)
- 仕掛り(つくりかけの製品)