モノづくりの現場における5Sは、すでに当たり前にできている会社や工場も多いとは思いますが、なかなか徹底できなくて悩んでいる職場も多いのではないでしょうか。
私自身も5Sを徹底できているかというと、時には手を抜いてしまうこともあります。3S徹底とスローガンを掲げ取り組み始めた頃はよいけれど、それが半年、1年と続くとマンネリ化や「これぐらいいいか」といった感じで、継続的改善どころか3Sの維持さえもあやしくなってくるのが続けることの難しさだと思います。
ここを乗り越えると習慣になり、後戻りしなくなると考えていますが、何事でも「続けることができる」のはやはりすごいこと、素晴らしいことだと思います。
さて、製造、モノづくりの現場においては、安全第一、そして、まずは3S(整理、整頓、清掃)を徹底することがポイントであると考えています。ご存知のように、3Sに加え清潔と躾の2Sを加えて5Sとなります。5Sの徹底は、モノづくりの現場での事故防止にもつながります。
また、業務改善や効率化視点なら、「ムダ、ムラ、ムリ」をなくそうになるのでしょうが、5Sができてからの取り組みでもよいと考えています。もちろん、「ムダ、ムラ、ムリ」を取り除いていけば、整理・整頓などの5Sの改善にもつながります。
どちらが先かということであれば、「ムダ、ムラ、ムリ」の前に、5Sのうちのまずは3Sに取り組むのがよいのではないかということです。
5Sの意味についてはネットでもいろいろと出てきますが、Wikipediaから引用します。
- 整理(せいり)
- いらないものを捨てる
- 整頓(せいとん)
- 決められた物を決められた場所に置き、いつでも取り出せる状態にしておく
- 清掃(せいそう)
- 常に掃除をする
- 清潔(せいけつ)
- 3S(上の整理・整頓・清掃)を維持し職場の衛生を保つ
- 躾(しつけ)
- 決められたルール・手順を正しく守る習慣をつける
製造の役割。図面からリアルなモノへ
製造現場では、図面や仕様書から素材(材料)を加工してモノを作ります。コンピュータの中の設計データ(図面)が、実際のモノとして姿を現すわけです。
よくある行き違いに、
- 設計側は、図面通りにモノができると思っている。
- 製造側は、図面通りにモノができるとは思っていない。
ということがあります。
良い例が思い浮かばず恐縮ですが、例えば、ステンレスの円板を作ることを考えます。図面では真円(まん丸)ですが、ステンレス板から切り出した(加工した)円板は、当然ながら真円ではありません。レーザー加工機を使えばほぼ真円にはなりますが、あくまでもほぼです。
しかも、大量に製造すればばらつきが出ます。レーザー加工機のような加工精度の高い機械を使うと、ばらつきを小さくすることができるということで、ばらつきを無視できるほどに小さくできるということでばらつきがなくなる訳ではないのです。
実際の商品開発においては、試作がOKになってから量産用の試作を作り、量産試作がOKとなってから初めて量産に移ります。量産といっても初めは少ない数量で、製造されたモノの品質が安定していることを確認しながら段階的に大量生産に移ります。
また、実際にモノを作ってみて初めて分かることがあります。モノを作ることによって見落としていたことが見つかることもあります。経験が蓄積されればある程度それらを予測することができるようになります。
つまり、製造側から見て分かる気づきや改善点があるのです。この知見、ノウハウを設計・開発や営業にフィードバックすれば、お客様への次の提案に役立てることができます。この様な好循環が生まれるのは、このような地道な活動の結果なのだと思います。
製造におけるポイント:自工程完結。
資材・部品購入から入庫(倉庫に保管)までの主なプロセス(工程)は、以下のようになります。
- 資材・部品購入
- → 受入
- → 保管
- → 資材・部品出庫
- → 製造
- → 完成品検査
- → 入庫(倉庫に保管)
入庫することで、完成品は製造部門から製品保管・出荷を担当する物流部門に移ります。
これらの工程(プロセス)のどれか1つでも10点満点で9点の工程があると、合格点である10点の製品をお客様に納めることができません。ある工程のマイナス点を、他の工程で挽回する(取り戻す)ことはできないからです。
自分が担当した工程のミスは自分の工程で発見し修正するのが原則です。次の工程で前工程のミスに気づくことがあるかもしれませんが、それを期待してはいけません。自分の工程で10点満点のモノのみを次工程に流すことがポイントです。
また、失敗したら同じことを繰り返さないことが大切です。失敗した、不良品を作ってしまったなら、その原因をよく考えて(分析し)、同じ失敗を繰り返さないように対策します。
さらに、その対策が有効かを確認・評価し、類似の工程に展開(横展開)していきます。
これを続けていけば、失敗が減っていくことは理解できると思います。その場限りの対応を続けていると、本当の原因が分からなくなりますし、不良品となってしまう兆候にも気づかなくなってきます。まさに、負の連鎖の始まりです。こうなると、どこから手をつけていいのか、どうにも手をつけようがなくなってきます。
製造におけるポイントは、次の2点だと思います。
1)異常時の対応
- 不良品を作るのを止める。
- 歩留まりが悪くなって後から選別すればよいと考えない。
2)ヒューマンエラーへの取り組み
- 「人はミスをする」ことを前提にして考える。
モノづくりの品質は各工程(設計開発、製造、出荷)の掛け算となることについてはこちら。
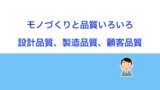
在庫管理と出荷:多品種・少量生産・短納期と変更管理
多品種、少量生産、短納期出荷が当たり前で、さらに、数量や納期の変更が発生すると、最終的に出荷担当部署への負担が増えることになります。
在庫についても、即納に偏りすぎるといわゆる不良在庫(長期滞留品)となり、売れるどころか処分するために追加費用が必要となることさえあります。
ここでは、在庫管理と出荷について考えてみます。入庫(倉庫に保管)から出荷までの主なプロセス(工程)に分けてみると、以下のようになります。
入庫(倉庫に保管):入庫することで、完成品は、製造部門から製品保管・出荷を担当する物流部門に移ります。
-
- 受注
- → ピッキング(倉庫から取り出す)
- → 梱包
- → 出荷
- この後は、
- → 配達(運送会社による輸送)
- → 納品(お客様による検収)
ここで、どのようなミスが起きているか上げてみると、
- 入庫時に入れる棚を間違えた。
- 棚から取り出す時に間違えた。
- 運送会社のラベルを貼り間違えた。
- 出荷日を間違えた。
といったように、人のミス、ヒューマンエラーがほとんどです。
人は間違えるので、これを前提に対策を考えていくことが必要です。
また、現場で何とかしろでは、なんともならないのが厳しい現実です。逆説的ですが、現場で何とかできるのなら、上記のようなミスは減っていくはずです。
作業手順書は、現場担当者が作るのが一番
例えば、作業手順を考える際にも、人はミスをすることを前提として考えます。
手順書は、実際に作業者が作るのが一番です。
ある工場の社長さんから、梱包時のミスがなくならず困っていたが、手順書を作業者に作らせたらミスがなくなったというお話を聞きました。
実際に手順書を見せていただきましたが、作業場で使うので大きめで、文字が少なく絵で説明してあり、初めてみても分かる手作りの分かりやすい手順書でした。
形だけの手順書はきれいで説明はしやすいかもしれませんが、現場では使わなくなるので作る意味がありません。
失敗を減らすためのポイントを列挙します。
- 現場で、当事者に考えさせる。
- 管理者(上長や社長)は、これをサポートすることに徹する。(相談にはのるが指示しない、口を挟まないのがポイント)
- 指示したことは、必ず確認する。
- 習慣化するまで、毎日、毎週、毎月、抜き打ち、様子をみながら注意喚起を続ける。
- 習慣になっても抜き打ちで確認、注意喚起を忘れない。
失敗を防ぐ対策が難しいわけではなく、徹底すること、続けることが難しいのです。
まとめ
モノづくりの現場において5Sを徹底できなくて悩んでいる職場も多いかと思います。5Sに限らず、半年、1年と続くとマンネリ化や「これぐらいいいか」となりがちで、習慣化するまで続けることができるのは素晴らしいことだと思います。
製造、モノづくりの現場においては、安全第一、そして、まずは3S(整理、整頓、清掃)を徹底することがポイントで、5Sの徹底は事故防止にもつながります。
また、業務改善や効率化視点なら「ムダ、ムラ、ムリ」をなくそうになるのでしょうが、5Sができてからの取り組みでもよいと考えています。どちらが先かということであれば、「ムダ、ムラ、ムリ」の前に、5Sのうちのまずは3Sに取り組むのがよいのではないかということです。
ここでは、以下について説明しました。
- 製造の役割。図面からリアルなモノへ
- 製造におけるポイント:自工程完結
- 在庫管理と出荷:多品種・少量生産・短納期と変更管理
- 作業手順書は、現場担当者が作るのが一番