ISO9001:2015でもヒューマンエラーに対策が求められています。
人が原因で起こるエラーだからヒューマンエラー、言葉遊びではありませんが、人はミスをするのでヒューマンエラーをゼロにすることは難しいことなのですが、それでもヒューマンエラー削減のため日々様々な対策が行われています。
ここでは、ヒューマンエラーの防止についてヒヤリハットを含めて説明します。
ありがちなヒューマンエラーの例
ヒューマンエラーによるクレーム事例と対策例を紹介します。
- AさんがX製品の梱包作業をしていたところ、急ぎの電話が入ったため、AさんはBさんに作業を依頼しました。
- 梱包品の中に外見が似たものがあり、確認モレにより間違った製品を梱包、出荷してしまいました。
この誤出荷について次の様な対策(再発防止策)を実施しました。
- 梱包要領に見て分かるように、写真と注意書きを加えた。
- 構成品の不足や違いを見て分かるように、X製品の構成品を梱包箱のどの位置に入れるか決め、梱包要領に写真と注意書きを加えた。
さて、これでご出荷を防ぐことはできるのでしょうか?
いずれの対策も人が注意する対策です。何らかの理由により、例えば不慣れな人が梱包作業をすることになったら、見て分かるようになっていても見落としが発生する可能性は残ります。
だからと言って、このケースではこれ以上の対策は現実的には難しいと考えています。人のミスを完全に防ぐためには、人が判断しないようにするしかないからです。
ISO9001の求めるヒューマンエラー対策
ISO9001:2015の要求事項では、ヒューマンエラーについて、
8.5.1 製造及びサービス提供の管理
g)ヒューマンエラーを防止するための処置を実施する。
どうやってヒューマンエラーを防止するかは、組織(会社)に委ねられています。
次にヒューマンエラー対策について、考えてみます。
ヒューマンエラーを防止するための対策
ヒューマンエラーを防止するための考え方として、
- 人はミスをするものだということを認識することからスタートする。
というものがあります。
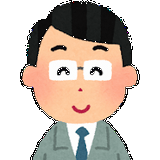
ヒューマンエラーの対策でよく見られるダブルチェックですが、「ダブルチェックは対策ではない」と言われるとそれはその通りなのですが、現実的にとれる対策がなく沈黙するしかないこともあります。
ここで、ヒューマンエラー(人的ミス)について調べてみました。
ここでは、以下の資料から引用します。
引用先:厚生労働省のホームページから「生活衛生関係営業の生産性向上を図るためのマニュアル(基礎編)(PDF)」
上記資料によると、ついつい・うっかり型の人的ミスは、下表の通り4つに分けることができます。
表1 ついつい・うっかり型の人的ミスの種類
人的ミスの種類 | 内容 |
---|---|
記憶エラー |
覚えられない 正しく続けられない 思い出せない |
認知エラー |
見逃す・聞き逃す 見間違える・聞き間違える 認識を間違える(思い込み) |
判断エラー | 今、どんな状況か、次に何をすればよいかの判断を間違える |
行動エラー |
方法を間違える 手順を間違える |
上記表の人的ミス、どれも思い当たることがあるのではないでしょうか。
上記厚生労働省の資料「生活衛生関係営業の生産性向上を図るためのマニュアル(基礎編)」には、ヒューマンエラーについての説明や対策についても丁寧に書かれておりお勧めです。
ヒヤリハット事例報告の利用
ヒヤリハットは事故防止のための活動でもありますが、その原因にヒューマンエラーがあることも少なくありません。
また、
「◯◯だったから事故にならずにすんだ。」
ということは、
「もしも、××だったら事故になっていた。」
ということでもあり、結果的に事故にならなかっただけのことだと考えることができます。
ヒューマンエラーを減らすためには、過去に起きた失敗事例を残して、振り返り、分析して、これからの活動に役立てることが効果的であり、事故を未然に防止するヒヤリハットの活動と共通する部分もあります。
ヒヤリハットの事例報告の目的
ヒヤリハットは、起こりうる事故を防ぐための活動です。
このためには、次の2点がポイントになります。
- できるだけ多くのヒヤリハットを報告してもらう。
- 記録を残して、分析、活用できるようにする。
これは「安全第一」にも通じることですが、
- 事故にならなかったからいいやと思う。
ではなく、
- 今回はたまたま事故にならなかっただけで、今後も事故になる可能性があると考える。
ことが重要になります。
つまり、ヒヤリハットは、
- 事故にはならなかったが、事故になる可能性のある事象(出来事)を発見できた。
ということであり、今後のための貴重な改善の機会でもあります。
仮に、ヒヤリハットが共有されない場合には、
- Aさんが経験したヒヤリハットが、Bさんに共有されず事故になってしまう。
事になりかねません。つまり、ヒヤリハットは作業者全員が情報を共有することが重要です。
ヒヤリハットは、ISO9001:2015で要求されている「7.1.6 組織の知識」にも含まれる内容です。
ヒューマンエラー、ヒヤリハットが、それぞれ別のものや活動ではなく、その情報を共有することで、事故の未然防止にも役立つという視点が重要です。
気づき(違和感)と行動
日頃様々な仕事をしていますが、何となく違うといった違和感を感じた経験がありませんか?
ここでは、違和感による気づきと行動について説明します。
作業工程における気づき(異常:常と異なること)
作業工程における気づき(異常:常と異なること)には、次の様なことがあります。
- 加工時の音がいつもと違う。
- いつもより見た目が悪く感じる。
- なんとなく違和感を感じる。
上記のような異常に気づいても具体的に説明できないので、それを聞かされる方は困ったことになったなと思うかもしれません。
しかし、現場の作業者はその作業のベテランです。常にその作業をしているからこそ、いつもと違う変化についてはとても敏感です。いつもと違う変化や気になることがあったら、作業者は自ら判断するのではなく、まず責任者に知らせて、判断を仰ぐようにすることが重要です。
実際に行っている作業からの気づき(予防)
品質問題が発生する恐れのある状況(違和感)には、次の様なものがあります。
- 何かいつもと違う。
- 異常ではないが何か変だと気づく。
経験値の高い現場作業者は、異常ではないのですが、いつもと違う状況になった際に、こうなったらこうするといった(対応、調整、工夫)をして、結果として品質に影響が出ないようにしていることがあります。
これらは、意識的というよりは、無意識に行っていることも多いようです。
経験から得た知識を、作業者個人の知識から、現場作業者全体、ひいては会社の知識として共有すると、それは会社にとっての強みにもなります。
例えば、冒頭のクレーム事例に例えるならば、
- 製品を梱包する前に、見た目が似ている製品を並べて種類と数量を確認してから箱に入れている。
といったようなことです。当たり前のことのように思いますが、そうではないということがポイントになります。
作業手順書作成のポイント
手順書作成のポイントは、
- 実際の作業者が作成すること
になります。
作業手順書は、それを使う作業者にとって分かりやすいものでないと、使われなくなります。
きれいな手順書である必要性はなく、作業者にとって分かりやすくミスをしないで済む手順書が良い手順書です。
一例ですが、組立ミスの対策として様々なことを行ったがミスがなくならず、困った社長さんは、「最終的に作業者に手順書を作成させたところ、ミスはなくなった。」そうです。
手順書を見せて頂くと、画用紙に手書きで、組立手順を図を使って説明したもので、間違えやすいポイント(どこで形状を見分けるか)が簡単な図で説明されていました。
別の見方をすれば、組立ミスをなくすことを、作業者が自覚して取り組んだからこそ手順書が必要と思い作成し、自分が使う手順書だからパッと見て分かるのだといえます。
つまり、一般的な手順書の作成ポイントは次の2点になります。
- 各作業工程(プロセス)において、ミスしやすいことを考慮して必要な対策を明確、具体的にする。
- 作業手順は、作業者(初心者)が見て分かるようにする。
繰り返しになりますが、作業者は手順書を見ながら作業をします。初心者が手順書を見て作業できなければ、近くの作業者に聞く、上長に聞くことになり、結局手順書は使わなれなくなってしまいます。
また、1ページに小さい文字で注記を加えても、特に初心者は落とします。どこに注意すればよいか分からないからです。
このため、手順が分からない、何か疑問に思うことが起きた場合にどうするかを明記しておくことが重要です。
ミスやクレームが発生するのは、いつもと違う状態(4M)の時が多いと言えます。急ぎの仕事、いつもよりも量が2倍とか3倍あり通常の手順では終わりそうにないといった場合に大きなミスが起きていることが多いです。
チェックリストのポイント
作業の抜け漏れを防ぐためにチェックリストが使われます。
チェックする作業に応じてチェックリストの項目数やチェック内容は変わってきますが、次のことを意識していますか?
- 何のためにチェックリストを使うのか?
- 抜け漏れを防ぐためには何を確認するのですか?
- 外観とか構成などの検査に近い内容を含んでいますか?
チェックリストを目的に応じた項目を具体的、かつ、明確に表現してあいまいさを無くすことが大切です。
例えば、不十分とか注意するといった表現は、人によってその内容が違いますので、具体的な表現にします。
また、チェックリストが使いやすいかにも配慮が必要です。
- チェックする手順に項目を並べてチェックしやすくする。
- チェックした結果を記録しやすくする。
といったことがポイントになります。
参考:チェックの原則と工夫の例
チェック漏れには、次の様な例があります。
- 出荷品が揃っていないのにダブルチェックのサインをしてしまった。
- ダブルチェックのサインがあるので、未チェックの品目があるのを見逃した。
- いつも同じ出荷先なので、出荷先の違いに気づかなかった(出荷先の欄を見ていなかった)。
下表に示すチェックの原則とチェック方法を考慮して、チェックリストを作ったり、チェックをすることが重要です。
表2 チェックの原則とチェック方法の例
チェックの原則 | チェック方法の例 |
---|---|
確実なダブルチェック |
|
チェック項目の明確化 |
|
チェックの形骸化を防 |
|
慣れに流されない工夫 |
|
まとめ
人が原因で起こるからヒューマンエラー。モノづくりに限らず古くて新しい問題でもあります。
ここでは、ヒヤリハットからヒューマンエラーを防止するための対策(異常に気づく、手順書やチェックリストの作成)などについて以下の項目で説明しました。
- ありがちなヒューマンエラーの例
- ISO9001の求めるヒューマンエラー対策
- ヒューマンエラーを防止するための対策
- ヒヤリハット事例報告の利用
- ヒヤリハットの事例報告の目的
- 気づき(違和感)と行動
- 作業工程における気づき(異常:常と異なること)
- 実際に行っている作業からの気づき(予防)
- 作業手順書作成のポイント
- チェックリストのポイント
- 参考:チェックの原則と工夫の例