ISOを導入したのにうまく回っていないケースは、業界や会社の規模にかかわらず、口にこそ出しませんが内心思っていたりと意外に多いようです。
設計・開発プロセスに定評のあるISO9000を導入したのに、
- 製品・開発はトラブル続きで発売が遅れる。
- ようやく出荷すると今度は、クレームが発生する。
モノを作っている以上、トラブルやクレームをゼロにするのが難しいことは分かっているのだが、「品質マニュアルと関連規定」に基づき原因を調べ対策をしているのに、
- トラブルやクレームが繰り返される。
- トラブルやクレームが増えているようにさえ感じる。
のはなぜなのか?
しかも、これは設計・開発を担当する技術や工場だけの話ではありません。
上記の疑問や悩みは、社長さん、設計・開発の部長さん、工場長、営業、商品企画、管理部門に至るまで、モノづくりメーカー内で共通のボヤキになったいます。
トラブルやクレームが発生すると、
- うちの技術がミスしまして・・・。
- 工場のミスで・・・。
- (新製品開発プロジェクトであれば)商品企画はなにやってんだ。
等々、社内の力関係でどこかの部署は沈黙せざるえないのですが、よくある話のようです。
そこで、モノづくりにおける設計や製造トラブルについて、私が経験したことやモノづくりの現場で見たり聞いたりしてきたことの中から共通することはないのか考えてみました。
モノづくりの3大トラブル
モノづくりにおける設計や製造トラブルの原因は、大きく次の3つに分類することができます。
- 新規設計により発生するトラブル
- トレードオフにより発生するトラブル
- 何らかの変更により発生するトラブル
発生するというよりは、設計(例えば図面)通りモノを作ってトラブルとなることもあり、起こるべくして起きているということでもあります。
設計者はトラブル内容に注意はしているのでしょうが、担当者任せであったり、確認モレなどの人的要因(ヒューマンエラー)でも設計トラブルは発生してしまいます。
これは、私の限られた経験でのイメージですが、クレームが発生した場合、
- 新規開発は、ほぼ100%クレームが発生する。
- コストダウンは、ほぼ100%クレームが発生する。
- 設計変更は、クレームにならなければ、お客様に言われなければラッキー。
といったイメージがあります。
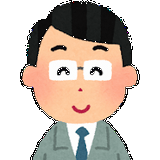
だからこそ、設計を再開発しないといけないなと思い、どうしたらよいのだろうと悩み、考えています。
以下、それぞれについて説明します。
新規設計により発生するトラブル
ここでいう新規設計には、次のような内容になります。
これまでと何か違っていれば「新規設計」と考えると、抜けや漏れが防げます。
- 新規技術(自社にとって初めての技術)
- 新規設計(従来の設計とは違う設計)
- 新規ツールの導入(設計や製造に限りません)
- 新規材料(新開発もあれば、製造中止に伴う変更も含みます)
- 新規メーカーの採用(製造委託先、設計委託の場合も含みます)
トレードオフにより発生するトラブル
ここでいうトレードオフは、設計品質の優先順位に関することです。
優先順位の変更そのものが問題なのではなく、優先順位を変更する理由により発生するトラブルになります。
トレードオフにより発生するトラブルについて、新製品でコストを重視したためクレームが発生した例で説明します。
【不具合(クレーム)内容】
従来品は、耐久性を重視して下表の部品Aを選定していました。
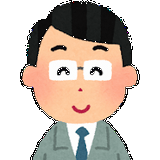
下表は、分かりやすくなるようかなり単純化しています。実際は入手性、納期も関係してもっと複雑ですが、本質的には同じことと考えています。
耐久性(カタログスペック) | コスト(部品の価格) | |
---|---|---|
部品A |
10,000時間 |
1個100円 |
部品B | 5,000時間 | 1個95円 |
新製品ではコストを重視して部品Aを採用しましたが、製品を使い続けていると故障が発生しクレームが発生しました。
原因を調べてみると、故障原因としては、
- 実際の使用条件において部品Bの耐久性(連続使用回数)がカタログスペック以上に低かった。
といったことが考えられ、これに気づかなかった原因を考えてみると、次のようなことが分かりました。
- 部品Aと部品Bの耐久性(連続使用回数)の比較は、カタログスペックのみで判断した。
- 耐久性(連続使用回数)について部品Bの確認をしていない。
- そもそも、その部品に求められる耐久性(連続使用回数)が、どの程度の仕様(実力値)があるか分からず、結果オーライで使っていただけだった。
これからどうするのか聞いてみようとしても、次の様な心の声が聞こえてくるようです。
- 言ってることは分かるけど、1つ1つの部品まではとても無理です。
- 部品をどの様にして決めたかは分からない(知っている人もいない)。
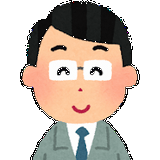
少々乱暴ですが、「設計していない」ということになります。
「設計」の意味が違うのかもしれません。
市場に出してからのクレームは、すでに出荷した製品の返品・交換対応費用だけでも、おそらくこの製品単体の利益はなくなってしまいます。
直接見えない会社のダメージとしては、信頼性の低い製品◯◯社というイメージダウンなども実際にはあります。
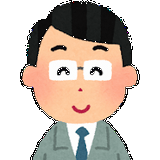
記憶があいまいですが「がっちりマンデー!!〜日曜に勉強!月曜から実践!〜」に出た食品メーカーだったと思いますが、新製品には絶対の自信をもって出荷するという会社の例もあります。
クレーム発生時の対応は、信頼性という面でその会社のビジョンそのものが評価される(試される)ものだと考えています。
何らかの変更により発生するトラブル
新規設計よりも幅広い意味での変更により発生するトラブルのことです。
購買(調達)であれば、
- 仕入先変更
- 材料変更
製造であれば、
- 工程変更
- 担当者変更
があります。
変更の理由は様々ですが、変更がないことを原則とするのではなく、変更があることを前提条件として、購買(調達)や製造を計画していくことが必要だと考えています。
モノづくりの3大トラブルの例とレビュー(トラブルの振り返り)
モノづくりの3大トラブルについて説明します。
設計思想につながるようなトラブル例とはなっていないため、製品不具合というより、新製品開発での社内トラブルのような内容ですが、要求と仕様にも関連すると思いますので、参考になれば幸いです。
- 新規設計により発生するトラブル
- トレードオフにより発生するトラブル
- 何らかの変更により発生するトラブル
新規設計により発生するトラブル例:PCとのインターフェース
スマホでは、簡易的ではありますが音声の収録機能(マイク)を使い、騒音計の様に音を計測するアプリがありますが、音を計測するためには、計測器の1つである騒音計を使います。
音や振動の他にもさまざまな計測器がありますが、計測器をハードウェアとして見ると、センサーと計測ユニットに分かれています。
- センサー
- 音や振動を検出する(計測する)。
- マイク、振動計、加速度や変位センサー
- 計測ユニット
- センサーで検出した電気信号をデジタルデータに変換する。
- パソコン
- センサーで検出し計測ユニットで変換されたデジタルデータを様々なデータに変換する。
- 信号処理やグラフ表示など
センサー、計測ユニット、パソコンの接続について整理します。
- センサーと計測ユニットとの間
- アナログ信号(電圧)です。
- 有線で接続します。
- 計測ユニットとパソコンとの間
- デジタル信号です。
- 無線でもよいですが、確実に信号を伝えるためには有線です。
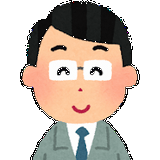
ワイヤレスの計測ユニットもありますが、センサー側でデジタル信号に変換されていれば、ワイヤレス、つまりデジタルで計測信号を飛ばしています。
ここで、計測ユニットとパソコンをつなぐインターフェース(接続ケーブル)について、困った問題が発生します。
計測上の要求としては、
- 確実にインターフェース(接続ケーブル)を固定すること
が必須となります。当たり前のことです。
計測ユニットは自社開発品なので、計測ユニットとインターフェース(接続ケーブル)の接続部分を作ることはできます。
しかし、パソコンとインターフェース(接続ケーブル)の接続部分は、パソコン用に部品のあるものを使うしかありません。
計測に使えるパソコン側のコネクタには次の様なものがあります。
- USB
- LAN
- IEEE1394(FireWire)
- PCカード(CardrBus)
- シリアル(RS232C)
計測器メーカーであれば、アナログ回路やデジタル回路の設計は得意ですが、パソコンのインターフェースとなれば別世界、まさに新技術です。
現実的には、USBかLANのどちらかを選択することになります。
計測する場合に確実な固定が必要ならば、コネクタにロック機構があるのはLANなので、LANに決定となるのですが、開発側の本音は、
- LANはこれまでの技術の延長上になく全くの新技術、LANについて調べるところから始めなくてはならないので、少なくとも今回の開発では無理だ。
- USBならこれまでの技術の延長線上で何とかなりそうだ。
というのが現状(現在の実力、力量)です。
そこで商品企画が次のような提案をして計測器用のUSBのインターフェースを開発することに落ち着きました。
- 実際にお客様がどのようにして計測しているか調べる。
- パソコンに接続するケーブルはすべて抜けないようにしていました。
- USBコネクタは抜けやすいのか振動試験をする。
- 試験対象や試験条件を決めるのもやっかいな問題ではありますが、振動試験では抜けないことが分かりました。
トレードオフにより発生するトラブル例:内蔵バッテリ
今どきの計測器は、計測ユニットとパソコンから構成されていますが、現場に出張して計測するお客様から、
- 現場に持っていける大きさ、重さなのはよい。
- 現場で電源を確保するのは仕方ない。
- パソコンと計測ユニットを接続するのに手間も時間もかかる。
- 現場で少し移動するだけなのに、計測ユニットのケーブルを外して、再接続は面倒。
という声が上がっていました。
こんな時に営業の大きな声と、商品企画の心の声を列挙すると、次のようになります。
- パソコン一体型の小型計測器は絶対売れる。(営業)
- 主力製品は売れてはいるが、新製品が絶対必要。(営業)
- 年間何台売れるのかと聞くと台数は絶対言わないんだよな。(商品企画)
- 一体型計測器のニーズがあることは確かだが、小型の一体型は今の技術では検討する工数も割けない。(商品企画)
こうして、一体型計測器の企画をまとめていく中で、小型の一体型は開発予算・期間からみて先送りとなりました。
一体型計測器の仕様で、最後まで問題となったのは「バッテリ使用時間」でした。
このバッテリ使用時間についての社内の意見は、
- 1日使える6~8時間
- バッテリ交換なしで2時間
ということで、世の中の技術からみれば実現可能だが、自社の部品調達やコスト面からは実現の見込みは、はっきり言ってなし。
しかも、社内意見はユーザーニーズではなく、自分が担当するお客様の声を要求と代弁しているだけなので、一体型計測器のイメージを深めることにはつながらないのでした。
また、一体型計測器に組み合わせるPCも、
- ノートPC
- タッチ型の業務用PC
など様々で画面サイズも違います。
結局、実物を触らせて次の2点を満たす業務用PCを選ぶことになりました。
- 現場で使うならマウスは使えないので指でタッチ操作できる。
- 計測用ソフトウェアは既存ソフトを使用する。
PCが決まると、問題になっていたバッテリ使用時間については、
- 20分程度
- 外部バッテリをつなげば、連続使用できる
というところに落ちつき、最終的に予想以上の出荷台数を記録したそうです。
販売後に営業が購入したお客様に聞いたところ、一体型計測器のメリットは、
- 管理が楽
- 現場で計測を始めるまでの準備が楽
- バッテリ駆動時間については、そもそもノートPC用に電源を用意するので気にしていない
というのが実際のユーザーの声だったそうです。
余談ですが、キャリングケースが欲しいということで、宅急便での輸送なども考慮してケースを作ったら海外旅行用のスーツケースの大きさとなりました。
これでよいというお客様もあれば、これではなということで、カート利用のお客様もあり、その後のビジネスバッグに入るサイズの一体型計測器を開発する際の参考になったそうです。
何らかの変更により発生するトラブル例:樹脂材料
樹脂製部品の対候性を上げるために、材料を変更したことによるトラブルになります。
技術的なレビュー(検討)が形式的なものだったために起きてしまった事例と考えています。
製品を出荷は10年以上前だったようですが、樹脂製の部品が経年劣化により割れているのが発見されました。
実際の使用期間は仕様書にある期間以上であり、メーカー側の問題ではなかったのですが、次の製品を開発するにあたり、従来品より対候性に優れた材料を選定し、さらに形状も一部変更しました。
シミュレーションの結果、従来の材料よりも最大応力値が大きいため、強度的に問題なしとの結論で開発したそうです。
そして数年後、新しい材料を使用した製品が経年劣化により割れているのが発見されました。
使用されている環境条件により経年劣化の状態は変わるので、対候性に問題があるとは一概に言えないのですが、気になったのは割れ方です。
従来品では、経年劣化により割れてしまえばその製品の機能は損なわれますが、ある部分が割れることで破片が飛散してしまうことはなかったそうです。
新製品では、経年劣化により割れた際に、複数の箇所が割れてしまうため破片が飛散してしまうようになりました。
割れ方が変わった可能性(原因)としては、次のような理由が考えられます。
- 新製品は、材料を変更したことで最大応力値は大きくなり、部品としての強度は向上している。
- 従来品は、割れても問題にならない特定の部分が割れるような設計になっていた。
- 意図してこのように設計していた訳ではなかったようです。
- 新製品は、形状を変更したことにより、複数の部分が割れるような設計となっていた。
つまり、設計審査(レビュー)において、材料変更による影響を最大応力値が従来品より大きくなっていたので承認したが、現場での使用上の要求という意味では、割れた際に部品が飛散しない割れ方をした方が望ましいということに気づいていなかったのではないかと考えることもできます。
参考:優先度を判断する基準
モノづくりでは、優先度を判断する基準として、
「どの様な品質のモノを、いつまでに、何個作るのか」
というモノづくりの品質、コスト、納期があり製品の3要素とも呼ばれています。さらに、自社開発か否かなどに関連する特許という要素もあります。
設計に関するものとしては、仕様書に定義される項目(仕様)であり、列挙されていることが多いと思われます。
当然のことなのですが、製品のイメージが具体的であれば、複数の項目の優先度が明確になるのですが、なんでもありは困ることが多いです。なんでもありの要求は、製品コンセプトもあいまいになり、販売面からもよいことはないと考えているのですが、なかなか伝わらないイメージがあります。
要素 | 補足説明 |
---|---|
品質(Quality) |
|
コスト(Cost) |
|
納期(Delivery date) |
|
特許(Patent) |
|
設計思想(設計に当たっての考え方)
設計思想というと難しそうに聞こえますが、製品の設計を始める(図面を描く前に)、どのような考え方で設計するか(図面を描くか)、設計する上での方向性(製品に対する様々な要求に対しどのような考え方で設計するか)を決めるものです。
設計思想は、設計に欠かせない考え方ですが、このブログ冒頭の悩みや疑問を抱える現場では、明確には意識されていないと思われます。
私の理解の範囲ではありますが、主な設計思想について、以下にまとめます。
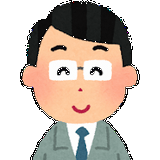
設計思想というと難しそうでとっつきにくいのですが、設計にあたり次のような項目の何を優先するのか、順番をつける考え方のことであると考えています。
- 安全性
- 低コスト(生産性)
- 操作性(使いやすさ)
- 大きさ(小さければよいわけではない)
- 機能・性能(速度、連続使用時間)
- 信頼性(耐久性)
- 保守性(メンテナンス性)
- シリーズ展開
フールプルーフ(foolproof)
フールプルーフの例としては、次のようなものがあります。
- 例 プレス機のばかよけ(両手で操作しないとプレスできない)
- 例 自動車でブレーキを踏まないとエンジン始動できない。
- 例 電子レンジのドアを閉めないとレンジがスタートしない。
設計でフールプルーフを検証するということは、
- 製品の使用者が操作や取り扱い方を間違っても壊れない、危険にならない。
- 誤った操作や危険な使い方ができない構造や仕組みになっている。
ことを検証することです。
フールプルーフの基本的な考え方(設計思想)は、
- 使用者が操作や取り扱い方を間違えても壊れない、危険にならない。
- 誤った操作や危険な操作ができない構造や仕組みになっている。
ように設計することです。
セーフライフ(safe life)
セーフライフは安全寿命設計とも呼ばれ、メンテナンスを前提とした設計手法であり、次の様なものがあります。
例 航空機のランディングギア(着陸装置)
例 踏み台
セーフライフは、製品の構造やコストなどを理由にフェイルセイフを適用できない場合などに適用され、設計でセーフライフを検証するとは、
- 設計寿命内で致命的な故障をしないこと
- 安全率(向上)
などを検証することです。
セーフライフの基本的な考え方(設計思想)は、
- 人の命が係わったら、まずはセーフライフを検討する。
- 設計寿命内で致命的な故障とならないように設計する。
- 安全率を向上させる。
ことです。
フェイルセイフ(fail-safe)
フェイルセイフの例には、次のようなものがあります。
- 例 自動車のパワーウィンドウを閉めたときに、身体が挟まれたらウィンドウが停止する。
- 例 手術室で、停電により電源が落ちた場合、自動的に非常用電源に切り替わる。
設計でフェイルセイフを検証するということは、
- 製品の一部(部品)が壊れても、製品全体の致命的故障にはならない
ことを検証することです。
フェイルセイフの基本的な考え方(設計思想)は、
- ある製品の一部(部品)が壊れた場合に、製品全体としては安全側になるように設計し、このために瞬時の停止や判断をする。
ことです。
ダメージトレランス(damage tolerance)
ダメージトレランスは損傷許容設計と呼ばれ、航空機の例しか思い浮かばないのですが次の様なものがあります。
- 例 戦闘ヘリのメインローターは、被弾してもローターが破壊することなく基地に戻ってからメンテナンス(交換)する。
設計でダメージトレランスを検証するということは、
- 製品の一部(部品)が壊れても、ひとまず製品の安全性や機能が失われずに維持される。
- その後、適切な期間経過後(必要とされる期間使い続けた後)、メンテナンスを行う。
ことを検証することで、
- 事前に製品を構成する部品が損傷した場合に、その損傷がどの様に進むかを予測する。
必要があります。
ダメージトレランスの基本的な考え方(設計思想)は、
- ある製品の一部(部品)が壊れた場合でも、引き続きその製品の安全性や機能が発揮されるように設計し、
- このため製品の一部(部品)の損傷がその後どの様に進むかを予測して設計する。
ことです。
モノづくり(4M変更)と製品トラブル
モノづくり、製造の現場であれば、3S、整理・整頓・清掃が基本です。
このモノづくりに必要不可欠な要素として、次の4Mがあります。
- ヒト(Man)
- モノ(Material)
- 設備(Machine)
- 方法(Method)
製品の3要素、品質、コスト、納期は、4Mにより大きな影響を受けます。
このため、製造の現場では、今日の4M変更について掲示板に掲示するなどして、作業者に周知・徹底するような工夫がされています。
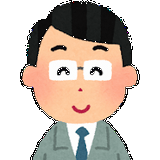
「4Mの変更はある」という前提で、4M変更の周知・徹底を行うというのがポイントです。
製品の品質、コスト、納期(製造だけでなく、設計のスピードも含む)は、製品の競争力を向上させるために必須の要素です。
品質が低いと、コストや納期に直接に悪い影響を与えます。
製品の製造中に4M(ヒト、モノ、設備、方法)の変更は、品質、コスト、納期に大きな影響を与えます。
例えば、製造するヒト(作業者)が替われば、
- 品質が変わります。
- 製品の生産性(数量や歩留まり)のコストが変わります。
- 製造のリードタイムの納期が変わります。
4M変更については、以下の記事をご参照ください。
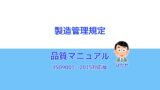
まとめ
モノづくりの設計や製造で繰り返されるトラブルについて、自ら経験したこと、見たり聞いたりしたことの共通点について考えてみました。
ここでは、以下の項目についてまとめています。
- モノづくりの3大トラブル
- 新規設計により発生するトラブル
- トレードオフにより発生するトラブル
- 何らかの変更により発生するトラブル
- モノづくりの3大トラブルの例とレビュー(トラブルの振り返り)
- 新規設計により発生するトラブル例:PCとのインターフェース
- トレードオフにより発生するトラブル例:内蔵バッテリ
- 何らかの変更により発生するトラブル例:樹脂材料
- 参考:優先度を判断する基準
- 設計思想(設計に当たっての考え方)
- フールプルーフ(foolproof)
- セーフライフ(safe life)
- フェイルセイフ(fail-safe)
- ダメージトレランス(damage tolerance)
- モノづくり(4M変更)と製品トラブル