「検査でモノの品質はよくならない」のですが、ここでは製品検査について説明します。
メーカーの検査は、「設計通りにモノができているかの確認をすること」になります。
完成してしまえば、分解しないと検査できないこともありますので、検査までの各プロセスが100%できていることが前提です。
品質が良くないと言いますが、その理由は様々です。
- 力量
- 図面が間違っているのは論外としても、製作方法が図面から読み取れない。
- 管理、マネジメント
- 修正された図面や製造工程の指示が、現場に届かない。
- ヒューマンエラー(人的なミス)
- 作業の確認漏れ
- 製作上のミス(3Hとか)
- 4M変更に起因するミス
- 検査漏れ(目視確認、抜き取り検査)
なぜ、検査で品質は良くならないのか、モノの品質に変わりはなく、検査では不良品を選別して流出を防いでいるだけだからです。
製品検査とは
メーカーの品質保証部門が担当している検査は、出荷前検査、最終検査とも呼ばれています。
検査では、図面や仕様書通りに商品が作られているかを最終的(出荷前に)に確認し、出荷を許可します。
検査員が、図面や仕様書に基づき作成した検査規格に基づき、
- 寸法(長さ、直径)
- 重さ
- 塗装の色、厚さ
- 外観(キズなど)
などを検査(確認)し、最終的な製品としての合否判定をします。外観に美観が入り込むと人による判断が難しくなります。
検査の目的と検査基準
検査の目的
- 顧客要求・ニーズに適合した製品であることを確認する。
- 出荷された製品が顧客ニーズに適合した製品であることを証明する。(検査記録や成績書:顧客に対する品質保証と、当社の保険という側面もあります。)
検査基準
検査員が判断しているのは、検査基準に従い、合格か不合格かであり、モノの品質の判定をしているわけではありません。
マニュアル記載の一例を示します。
- 「検査」とは、品物を検査した結果(寸法、塗装厚、外観等)を、品質判定基準(検査規格)と比較して、個々の品物の良品・不良品の判定を下し、又はロット判定基準と比較してロットの合格・不合格を下すことをいう。 検査には、次の判定がある。
- 個々の製品に対して実施する判定:良品・不良品の判定をする。
- ロットに対して実施する判定:抜取検査によりロットの合格・不合格の判定をする。
- 「検査基準」とは、その製品の要求から導き出される品質の基準をいう。製品間の相対的な比較によるものではない。
とはいえ、そうもいかない場合もあります。
例えば、めっきは防錆(さび防止)のための処理なのに、外観(美観)が要求されるようになってきており、クレームとはならなくても対応せざる得ない場合が増えていますが、コストは製造側持ちとか・・・。
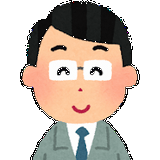
検査で品質は良くならないとの言葉は事実ですが、検査基準(規格)には何かと難しい面もあります。
検査員の仕事
検査員も新入社員、中途採用、ベテランと様々ですし、お客様が立ち会う立会検査、出張して現地で行う検査もあります。
毎日の検査
検査員としての心構えの1つとして、検査により図面通りの製品であるか判定し、「合格=図面通りの製品である」ことを保証する。これを証明するのが検査記録であることを忘れないことが上げられます。
検査員の業務フローは、次のようなものになります。
- 準備(出社、朝礼、その日の段取り)
- 検査業務(作業中断、割り込み対応)
- 不合格品の処置(返品、手直し等)
- 片付け(その日の振り返り、明日以降の指示など)
定期的な検査
会社によっては、毎月一定の出荷がある製品については、定期的に行う検査があります。
検査記録の管理
検査記録は、複数の拠点がある場合には、拠点ごと管理する場合と、本社の品質保証部で全社分を一括管理する場合とがあります。
検査記録の電子化(データベース化)は、システムによるか表計算ソフトによる人による管理かは別として必須になっています。
これにより、例えば、出荷後に製品の不具合(不良)が見つかった場合に、いつ・どこで製造・検査したものか追うことができます。(トレーサービリティといいます。)
まとめ
メーカーの検査は、「設計通りにモノができているかの確認をすること」であり、「検査でモノの品質はよくならない」のですが、ここでは製品検査について以下の項目について説明しました。
- 製品検査とは
- 検査の目的と検査基準
- 検査の目的
- 検査基準
- 検査員の仕事
- 毎日の検査
- 定期的な検査
- 検査記録の管理