異常とは「常とは異なる」こと、つまり「いつもと何かが違う」ことです。
モノづくりの現場では、何かが違うと気づいたり感じたりしたら速やかに上長に報告し、三現主義で現場で、現物を見ながら、現実的に検討し、情報を共有します。
大きな設備トラブルも、原因を調べていくと、現場では小さい異常(いつもと違う変化)に気づいていたことも少なくはないようです。
モノづくりの現場で、日々作業をしている現場の方が、最もいつもと違うことに気づきやすいものです。ここでは、異常の管理について、異常を見つけた人と上長(リーダー)の対応を含め説明します。
「異常」とは
ここでの「異常」とは、入荷工程、製造工程、検査工程で発見された、製品・部品の品質に関する全ての異常で、以下の2つに分けられます。
- 工程異常:作業や工程がいつもと違う。
- 品質異常:不良の発生がいつもと違う。
具体的な異常の例を以下に示します。
工程異常:作業や工程がいつもと違う
工程異常の例を以下に示します。
いつもと違う場合
異常の内容 | 具体例 |
---|---|
いつもと違う音、色、手触り、臭い等を感じた |
|
いつもと違う量、重さ、硬さ、精度(ばらつき)を感じた |
|
作業手順書どおりに作業してもできない |
|
設備やジグにいつもと違う現象が起きた |
|
おかしいと思った場合
異常の内容 | 具体例 |
---|---|
組付部品の過不足が判明した |
|
良品、不良品の判断ができない |
|
落下品があった場合
異常の内容 | 具体例 |
---|---|
部品や工具を落とした |
|
部品が落ちていることに気づいた |
|
管理図などのデータがいつもと違う場合
異常の内容 | 具体例 |
---|---|
工程内の計測データがいつもと違うことに気づいた |
|
品質異常:不良の発生がいつもと違う
品質異常の例を以下に示します。
異常の内容 | 具体例 |
---|---|
初めての不良 |
|
通常より不良数が多い |
|
いつも出ていた不良が出なくなった |
|
重点管理項目の不良 |
|
過去の不良と類似の不良 |
|
異常時の作業者と上長(リーダー)の役割
異常に気づいた時の作業者と上長(リーダー)の役割について説明します。
異常発生時の作業者の役割
異常に気づいた際の作業者の役割(行うこと)を以下に列挙します。
- 作業者は異常が発生したら、直ちに設備(ライン)を止める。この際、必ず安全処置を取る。
- 異常を報告した後は、現場リーダーの指示に従い、行動する。
- 決して、自らの判断で処置をしてはならない。
- 作業者は、異常が発生し、設備を止めた時は、処理済みの製品と未処理の製品の識別(区別)をする。
- 作業者は、「止める・呼ぶ・待つ」を徹底する。
上長(リーダー、管理・監督者)は、作業者からの異常の連絡を受けたら、関係者に連絡を行い、現物隔離等を確実に行います。
また、作業者が異常に気づいたにもかかわらず、「止める、呼ぶ、待つ」を実践しないと、
- 不良のまま製造が継続し、不適合品が増大(ロスも増大)してしまう。
ことを周知・徹底していくことがポイントです。
現場リーダーの重要な役割
現場リーダーとして、発生した異常の対応後に重要なことを以下に列挙します。
管理(PDCA)のサイクルを回し管理水準を上げていくこと
管理のサイクル(PDCA)による品質改善活動を進めます。
PDCAを小さく早く回し、段階的にPDCAの目標をレベルアップし、品質改善活動のレベルアップを図ります。
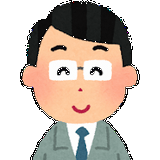
品質改善活動におけるPDCAによるスパイラルアップのことですが、現場でスパイラルアップと言ってもなかなか伝わらないようです。
現場(グループ)から作業者になればなるほど、具体的な作業にまで落とし込みが必要だと考えています。
異常を見える化すること
掲示板(管理ボード)に異常が発見された工程を掲示するなどして周知することにより、類似のミスが発生することを防止することができます。
標準化とPDCAをバランスよく進めることで、PDCAサイクルを繰り返し継続して回すことで、強い生産現場を作り上げていくことができます。
異常を早く知らせる雰囲気づくり
作業者が「何かおかしい」と気づいたら、速やかに上長に伝え、上長は何が起こったかを現場で聞くことで、異常を知らせることが改善につながる現場にしていくことができると考えています。
現場でPDCAと標準化を回すことで、継続的な改善が当たり前(普通)の現場になり、モノづくりに強い会社になっていくと考えています。
まとめ
異常とは「常とは異なる」こと、つまり「いつもと何かが違う」ことです。
大きな設備トラブルも、原因を調べていくと、現場では小さい異常(いつもと違う変化)に気づいていたことも少なくないようです。
モノづくりの現場で、日々作業をしている現場の方が、最もいつもと違うことに気づきやすいものです。
ここでは、異常管理について以下の項目で説明しました。
- 「異常」とは
- 工程異常:作業や工程がいつもと違う
- いつもと違う場合
- おかしいと思った場合
- 落下品があった場合
- 管理図などのデータがいつもと違う場合
- 品質異常:不良の発生がいつもと違う
- 工程異常:作業や工程がいつもと違う
- 異常時の作業者と上長(リーダー)の役割
- 異常発生時の作業者の役割
- 現場リーダーの重要な役割
- 管理(PDCA)のサイクルを回し管理水準を上げていくこと
- 異常を見える化すること
- 異常を早く知らせる雰囲気づくり