「品質マニュアル3.0」の関連規定の1つ、「製造管理規定」に関連する製造管理の参考のうち「製造の品質」についての補足資料です。
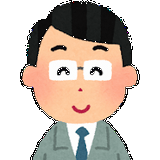
製造はしているが仕組みとして明確になっていない場合などに考慮すべき内容を含めています。
モノづくりが初めての場合のテキストは、以下のページにまとめています。
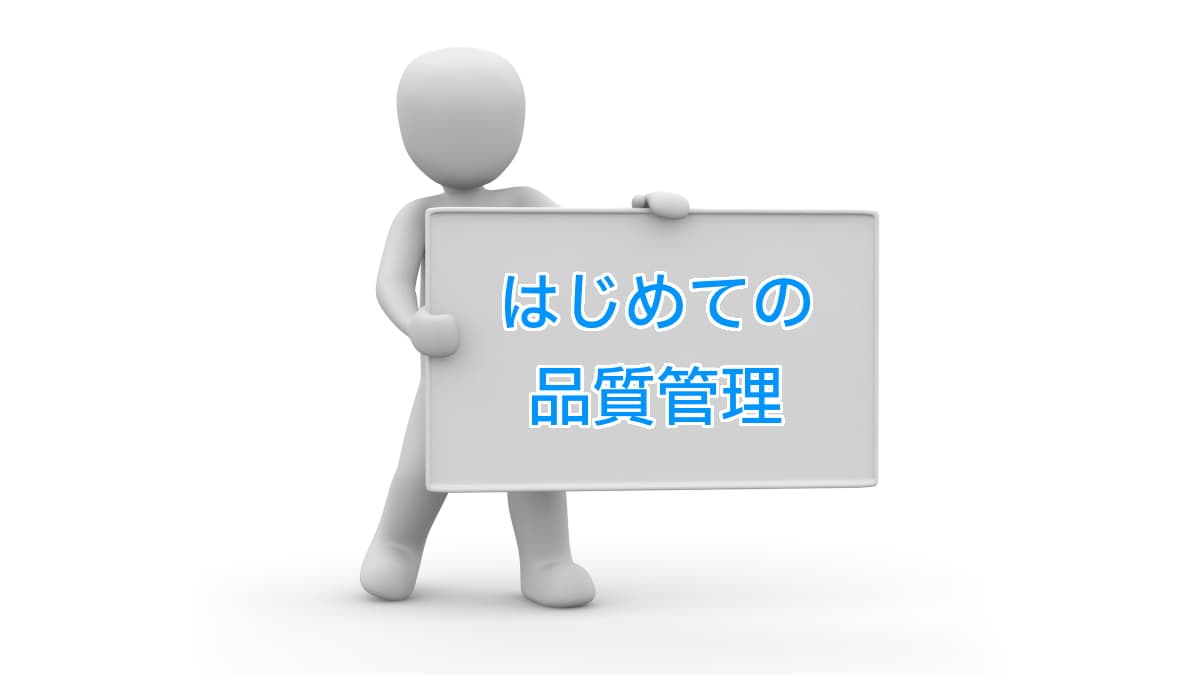
品質管理の心構え「次工程はお客様」とは
「次工程はお客様」は、品質管理で大事な標語です。
簡単に言えば「次の工程はお客さんと思い、良い品質ものだけ払い出すこと」となりますが、「次工程はお客様」は品質管理の心構えとして必須であるため、次の3段階に分けて説明します。
①「自分の工程での責任を果たす」
会社で働く人は全員、責任を与えられて仕事をしています。ですから会社で働く人全員が自分の工程での仕事の責任を果たさなくてはいけません。これを最初の工程から最後の工程まで全員が行えば品質の良い製品を作り出せます。
②「前工程は次工程に対して品質の責任がある」
前工程の品質が悪ければ後工程で品質の良いものを作り出すことはできません。自分の工程に責任を持つとは、次の工程に払い出す製品の品質を保証するということです。次の工程はお客様同様、品質の良い製品だけを払い出すようにします。
③「前工程からは品質の良いものしか受け取らない」
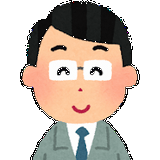
品質に良い悪いはありません。基準を満たしているか否か、合格品しか受け取らないということです。
前工程からは品質の良いものしか受け取らないようにします。また後工程は前工程に対して正しい品質の要求を行う責任があるのです。ですから不良はもちろん品質上、気がついた点は上司を通じて前の工程にフィードバックするようにします。
上記の3段階に分けることで、「工場で働く人全員が、自分の工程に責任を持って仕事を行い、お互いの工程で良いものしか払い出さない、受け取らないようにして行くことにより品質の良いものだけを作り出すことができるようになる」ことを理解する助けになります。
日常当たり前に使っている言葉ですが、説明するときは相手が具体的に何をすればよいのかが分かる説明の仕方を心掛けることが大切です。
変化点管理(4M変更管理、3H管理)による事故やトラブルの防止
製品の3要素(QCD)と製造の4M
製品を製造する場合に、「どのような品質のモノをいくらで、いつまでに何個作るか」、つまり、品質(Quality)、原価(Cost)、納期(Delivery)の3つの要素が求められ、「製品の三要素」と呼ばれている。
製品を製造するには、ヒト(Man)、モノ(Material)、設備(Machine)、方法(Method)が不可欠であり、「4M」と呼ばれている。
製品の3要素であるQCDは、次のように4Mによって大きな影響を受けるため、掲示板等により「今日の4M変更は何か?」を各4M変更項目ごとに見える化する、変化点定義を掲示する等、作業者に周知させるための工夫が必要である。
- 生産するヒト(作業者)が替われば、出来ばえの品質(Q)が変わり、製品の生産性(C)及び製造のリードタイム(D)が変化する。
- 製品のQCDは製品の競争力を向上させる上でも不可欠であり、なかでも品質(Q)の低さは、コスト(C)や納期(D)に悪影響を及ぼす。
- 製品の製造中に4M(要因系)に変更があった場合は、下図に示すように、製品の3要素であるQCD(結果系)に非常に大きな影響を与える。
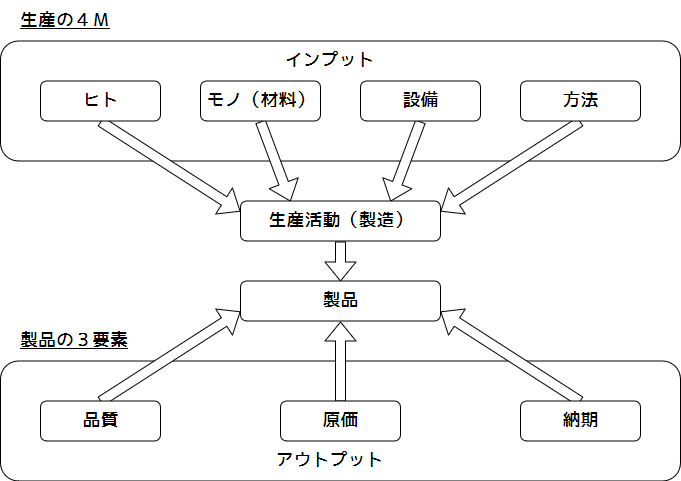
製品の3要素(QCD)と製造の4M
4M変更における変化点
(1)計画的変化点と突発的変化点
4M(ヒト、モノ、設備、方法)が変化する時点は、次の2つに分かれる。
計画的変化点 |
事前にかわることが分かるもの(人の配置、設備保全など) |
---|---|
突発変化点 |
突然起こり、予知できないもの(設備故障など) |
計画的なもの、突発的なもの、それぞれについて事前に変化点として明確にする。変化点の例を下表に示す。
分類 |
要因(4M) |
変動項目 |
---|---|---|
計画的変化点 |
ヒト |
作業者変更(一時交代含む)、 年次休暇、ローテーション、一時離業、短期離業復帰 |
モノ(材料) |
設計変更(材料変更、材質変更など)、新規材料の採用 材料の供給者変更、材料のグレード変更、材料の配合比率変更 |
|
設備 |
加工設備変更、改造・改修工事、定期点検、設備移設、工場移転 金型変更・更新、ポカヨケ装置(センサーなど)の変更・移設 工具・ジグ・刃具変更・交換、検査ジグ・ゲージ新設・更新 |
|
方法 |
作業手順変更、設備管理方法の変更 工程変更、条件変更(管理基準の変更)、 工法変更、ライン変更、タクト時間変更、仕掛変更 |
|
突発的変化点 |
ヒト |
一時離業(トイレなど)、突発的な休暇、ライン停止と再起動 |
モノ(材料) |
異常処置(後追い点検、さかのぼり点検)、 不具合品を流動せざる得ない場合 |
|
設備 |
設備故障・修理、設備異常、金型破損、 検査ジグの故障・破損、工具・ジグ・刃具の劣化・破損 |
|
方法 |
作業遅れ時の挽回、 作業ミス(条件設定ミス、段取りミス、ルール違反) |
|
その他 |
地震、台風、火災、停電など |
自社内及び外注先の変更点管理における注意事項
(1)変更については、社内複数部署にまたがる場合でも、漏れなく対応する。
(2)製造上の条件に変更がある場合は、必ず顧客に連絡および了解をもって、その製造条件で品質に問題がないか、顧客の要求事項通りの製品であるかを確認の上、出荷する。
(3)製造上のわずかな変更も、製造した製品に品質上の問題が発生する可能性はある。
(4)実際に「条件を変えても品質に問題ない」と思い製造した製品において、クレーム(品質問題)となるケースは少なからず発生している。このため、変更点(=製造での条件変更)での管理とチェックは、品質管理上重要なポイントである。
顧客には事前に条件変更の連絡を行い、必要に応じ顧客による製品確認を行い、顧客が了解・承認してから製造を開始する。
協力工場や外注先に製造を委託している場合は、協力工場や外注先に同様の管理を依頼する。この場合でも、顧客に事前連絡を行い、顧客による製品の品質確認後、製造開始(許可)の連絡を受けてから製造する。
(5)品質改善活動後に、管理水準や管理方法の変更が伴う場合がある。これは計画的な変更であり、品質工程図、作業標準、検査規格等の改版を行い、作業者への事前説明を行う。
(6)変化点管理では、変化点管理項目について事前打合せを行い、事前通知すべき内容を取り交わしておくこと。
(7)変更点管理対象項目の例
|
対象項目 |
事例 |
---|---|---|
1 |
外注先の変更 (2次以降仕入先含む) |
材料購入メーカー、加工メーカー、めっきメーカーなどの変更 |
2 |
材料の変更 |
材質、材料メーカー、材料グレード、副資材(溶剤等製品の一部にならないもの)、素形材(鋳造・鍛造・ダイカスト等で製造された素材)の変更 |
3 |
加工条件の変更 |
条件の変更(成型、溶接条件、めっき条件など) |
4 |
加工方法の変更 |
工法の変更 (例 アーク溶接→スポット溶接、切削→転造など) |
5 |
工程系列の変更 |
製造工程の追加・削除・分離・統合・順序の変更 |
6 |
機械設備の変更 |
機械設備の新設、変更、改造、工場の移動・増設など |
7 |
金型、治工具の変更 |
更新、改造及び品質に影響を及ぼす修理など |
8 |
検査方法の変更 |
検査機、検査ジグの変更 |
9 |
作業者の変更 |
重要工程の作業者の変更 |
10 |
梱包仕様の変更 |
梱包方法、梱包材料の変更 |
※4Mの変更品はきちんとロット表示を行い管理する。
理由:後日クレーム等で調査する範囲や処置する範囲を特定しやすく、ロスを最小限に食い止めることができるため。
(8)変更管理項目の例
項目 |
内容 |
|
---|---|---|
型の変更 |
新規の型 (新図面の型) |
新規図面で型を作成し使用する場合 |
型の部分的改善 |
型を改善し、今までの型と形状および寸法が変わる場合 |
|
型の修正 |
型の摩耗等により修正した場合 |
|
同じ図面の型 (更新) |
図面寸法は変わらないが、新しく作成した型を使用する場合 |
|
設備の変更 |
機械の変更 |
使用登録していない機械を使用する場合 |
設定・条件の変更 |
設備条件及び事件、物質(溶液など)を変更する場合 |
|
刃物の変更 |
刃物の形状及び型版、メーカーを変更する場合 |
|
刃物の再研磨 |
刃物の摩耗により再研磨した場合 |
|
ジグの変更 |
ジグの形状及び当て基準等を変更する場合 |
|
測定機器の変更 |
測定機器の種類を変更する場合 |
|
設備の移動 |
大型な設備を移動させる場合(レイアウト変更) |
|
加工先の変更 |
外注加工先を変更する場合、外注移管及び社内取り込みを行う場合 |
|
方案・方法の変更 |
工程の入れ替え |
工程の順序変更及び、追加、削除をする場合 |
作業内容が違う |
作業の要領を変更する場合 |
|
寸法及び公差の変更 |
規格寸法及び公差・基準の変更をする場合 |
|
測定内容の変更 |
測定方法で測定点・基準面等を変更する場合 |
|
材料の変更 |
材質の変更 |
材質を変更する場合(材料の形状変更も含む) |
メーカーが違う |
材料メーカーを変更する場合(同質材でも同様) |
|
人の変更 |
登録作業者以外 |
登録しているオペレーター以外が作業を行う場合 |
新人作業者 |
新人作業者が初めて作業を行う場合 |
3H管理
3Hとは
経験則として、事故やトラブルは3H(初めて、変更、久しぶり)の折に起き、定常時には極めて少ない。3H活動とは、これに着目し、事前に3Hの視点で課題に気付き、問題が発生しないように、確認しながら仕事を遂行する仕組みで、事故やトラブルを防ぐ活動である。
(1)3Hを必要とする背景
事故やトラブルの影響は深刻さを増しており、事故やトラブル発生の際は、その再発防止(是正処置)は必須であるが、事故や損失(ロスコスト)の結果行う再発防止ではなく、いかに防止するかが重要である。
事故やトラブルを防止する方法の1つに3Hがある。3Hは簡単で親しみやすい方法で、誰でもいつでもどこでも参加できる。まず、できることから取り組み始めればよい。さらに全員参加の活動に発展すると効果は絶大である。
(2)3H有効活用のポイント
3Hの基本は、仕事に着手する前に3Hの視点でいかに気づき着眼するか、そして、仕事のなかで確実に確認・実行するかに尽きる。モノづくりを例にした3Hを下表に示す。
製品実現 ・初めて ・変更 ・久しぶり |
人 |
・初めて ・変更 ・久しぶり |
新入社員(新卒、中途、パート、アルバイト) 配置転換(人事異動) 職場復帰(育児休業明け、療養復職) |
---|---|---|---|
機械 |
・初めて ・変更 ・久しぶり |
新規導入設備(機械、金型、ジグ等) 仕様変更、修理した設備( 〃 ) 半年以上不使用の設備( 〃 ) |
|
材料 |
・初めて ・変更 ・久しぶり |
新規使用材料 材料変更、材料メーカー変更 半年以上間隔があいて仕入れた材料・在庫材 |
|
方法 |
・初めて ・変更 ・久しぶり |
初めての作業(製作、検査、管理) 作業の変更( 〃 ) 半年以上間隔があいて行う作業( 〃 ) |
モノづくりでは「製品実現」が最上位にくる。製品実現には設計、製造、物流等のプロセスがあり、これらを4M(作業者、機械、使用材料、作業方法)の視点、さらに3H(①初めて、②変更、③久しぶり)の視点で目を向けていく。
次に業務フローに沿った3H実施要領を作成してルールとして定める。
基本は2つで、まず業務フローに沿って次々と進む仕事に対しての課題について、①だれが、②いつ、③どうするか、を決める。そして、一日、一カ月のなかで時系列に課題について、①だれが、②いつ、③どうするか、を決める。
例えば、部署長は月末に実行された3Hの、すべての「歯止め」の実行点検、「歯止め」のルール化の点検、ルールの見直しをして、3H活動報告をする等である。
3Hは、日常業務の徹底、そして5Sの充実などと共に実施すると大きな相乗効果が得られる。そして、品質不良ゼロ、納期遅延ゼロ、労働災害ゼロの実現に迫ることができる。
4Mと3H管理
製造現場で不良が最も多く発生するのは、製造条件を変更した時である。
4M(ヒト、モノ、設備、方法)の変更があった時は、初品検査を必ず行い後工程はしばらくの間は十分注意を払い製品をチェックする。これを初期流動監視という。
この監視するタイミングは、生産立上がり(初めて)、製造条件変更(変更)、再稼働(久しぶり)があり、これを「3H管理」という。
異常管理
「異常」とは
「異常」とは、以下の場合をいいます。
- 作業や工程(人・機械・材料・方法・計測・環境)がいつもと違う時(要因系の異常)
- 不良の発生がいつもと違う時(結果系の異常)
入荷工程、製造工程、検査工程で発見された、製品・部品の品質に関する全ての異常に適用します。具体的な異常の例を以下に示す。
(1)工程異常
作業や工程がいつもと違う時(要因系の異常)
項目 |
異常の内容 |
具体例 |
---|---|---|
①いつもと違う時 |
いつもと違う音、色、手触り、臭い等を感じた時 |
・めっきの色がいつもと違う ・キズ、割れ、欠け、汚れがある ・コンプレッサー音がいつもより高い |
いつもと違う量、重さ、硬さ、精度を感じた時 |
・ケースの重さがいつもより重い ・テープの硬さがいつもより硬い ・梱包状態が違う(整列→バラバラ) |
|
要領書どおりに作業してもできない時 |
・指定時間内に物ができない |
|
設備、ジグ等にいつもと違った現象が起こった時 |
・設備の異常ランプがよく点灯する。 ・設備の作動が通常より早い、遅い ・設備、容器内に残留品がある ・水、油の漏れを見つけた |
|
②おかしいと思った時 |
組付部品の過不足が判明した時 |
・員数をそろえた部品が足らない又は余った |
良品、不良品の判断ができない時 |
・限度見本では判断できない |
|
③落下品があった時 |
落とした時 |
・部品を落とした |
落ちていることに気づいたとき |
・通常落下していない場所に部品が落ちていた |
|
④管理図で点のならび方が異常を示したとき |
・限界線から点が飛び出した ・いつもと傾向が変わった |
(2)品質異常
不良の発生がいつもと違う時(結果系の異常)
異常の内容 |
具体例 |
初めての不良が出た時 |
・今までにない不良が発生した |
通常より多い不良が出た時 |
・時々しかでない不良が連続して発生 |
いつも出ていた不良が出なくなった時 |
・慢性的な不適合が急に無くなった |
重要な不良が出た時 |
・重点管理項目に指定されている箇所に不良が発生 |
過去に発生したものと類似の不良が出た時 |
・対策実施後、再び同じ不良が発生 |
異常時の役割(作業者、現場リーダー)
異常時の作業者の役割
・作業者は異常が発生したら、直ちに設備(ライン)を止める。必ず安全処置を取る。
・異常を報告した後は、現場リーダーの指示に従い、行動する。
・決して、自らの判断で処置をしてはならない。
・作業者は、異常が発生し、設備を止めた時は、処理済みの製品と未処理の製品の識別(区別)をする。
・作業者は、「止める・呼ぶ・待つ」を徹底し、管理・監督者はその連絡を受け、関係者に連絡を行い、現物隔離等を行う。
「止める、呼ぶ、待つ」を実践しなかった場合、不良のまま製造が実施され不適合品が増大(ロスも増大)してしまう恐れがあることを忘れないこと。
現場リーダーと作業者の主な役割の一例
現場リーダーの役割 |
作業者の役割 |
---|---|
作業標準(決め事)を作成する |
作業標準やルールなどの決め事を守る 不良品を後工程に流さない 設備、ジグなどを点検する |
作業者に標準作業を守らせる。 |
|
「作業手順や方法」の見える化を行う |
|
必要に応じ、作業標準を改訂する |
|
異常発見時のルールを作る |
異常発生時にラインを止め、管理者へ報告する 処理済みの製品と未処理の製品の識別(区別)をする |
異常発生時に対策の指示をする |
|
生産の4Mに気を配る 「変化点管理」を行う |
QCDを満足する製品を生産する |
5S活動の実施計画を作成する 活動の進捗状況を監視する |
5S活動の実施計画を実行する 5S活動状況を報告する |
製造活動の「ポカヨケ」を行う |
製造活動で「ポカミス」をしない |
現場リーダーの重要な役割
現場リーダーとして、さらに3つ重要なことを以下に示す。
(1)管理のサイクル(いわゆるPDCAサイクル)を回し管理水準を上げていくこと
品質改善活動をP(計画)、D(実施)、C(確認)、A(処置)の順に進め、次の1段高い目標のP(計画)へと繋げていきながら、活動のスパイラルアップを図る。
(2)異常を見える化すること
管理ボードにどの工程で異常が発見されたのかを掲載する等して、周知することにより類似のミスをできる限り防止する。
標準化はPDCAを回すための車輪と考え、このPDCAサイクルを繰り返し継続的に回すことにより、強い生産体質(企業体質)を構築することができる。
(3)異常を打ち上げる雰囲気づくり
作業者が何かおかしい、と気づいたときに何が起こったかを聞いてみて、異常の打ち上げに感謝する風土を培うことにより改善に結び付けることができる。
4M変更管理
4M変更管理を徹底すること。
禁止物質混入を防止するため、仕入先様にて原材料や副資材等を変更する場合には、事前に顧客に申請する。
禁止物質の有無を相互に確認(顧客、当社)し、顧客が許可した上での変更となる。
原材料の変更とは |
購入先の変更、めっき加工業者の変更、メーカー・品番等の変更、添加剤の変更、調合メーカーの変更など |
---|---|
副資材とは |
図面等で指定されていないが、部品・部材の製造過程にて使用し、かつ部品・部材の構成に必要なもの及び付着するもの 例 テープ類、マーカー(マジック)、修正塗料、洗浄剤、クリーナー、プレス等の加工油(脱脂なし)、離型剤、接着剤、インク、結束バンド、ハンダなど |
RoHS指令/ELV指令について
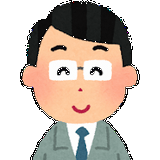
RoHS対応についての問い合わせがやっかいなのは、該当する物質が法令等のどの部分に書いてあるかがとても分かりにくいからだということをセミナーで知りました。
RoHS指令/ELV指令
RoHS指令/ELV指令は、EU(ヨーロッパ)の法律です。
違反すれば当局に摘発されるのみならず、製品の販売停止、改修、リワークなど莫大な費用が発生します。また、大手セットメーカーでは、即取引停止になる場合があります。
下表の他に、韓国版RoHS/ELV(2008年1月施行)、カルフォルニア2007年1月施行などもあります。
RoHS指令 |
(Restriction of the use of certain Hazardous Substances) [2006年7月施行]電気・電子機器に含まれる特定有害物質の使用制限 鉛、水銀、カドミウム、6価クロム、特定臭素系難燃剤(PBB、PBDE)の6物質に加え、2019年7月22日よりフタル酸類の4物質(DEHP、BBP、DBP、DIBP)が追加され使用制限物質は合計10物質になります。 |
---|---|
ELV指令 |
(End of Life Vehicles) [2003年7月施行]廃自動車指令による化学物質の使用禁止 鉛、水銀、カドミウム、6価クロムの使用禁止 |
中国版 RoHS指令 |
2007年施行、2016年7月改正中国RoHS管理規制施行 ・中国国内で電子情報製品を生産、販売、輸入する者が対象 ・対象有害物質(6物質+1物質)含有情報、安全使用期限の表示義務付け(第1段階) ・国家基準や業界基準に適合しない製品の輸入を禁止(第2段階) |
なお、禁止物質の含有リスクが高い製品について特に注意が必要です。高リスク製品の例を下表に示します。
高リスク製品 |
対象物質の用途 |
含有物質 |
---|---|---|
プラスチック製品 |
安定剤、顔料、難燃剤 |
Pb、Cd、Cr+6、PBDE |
ゴム成形品 |
||
塩ビリード線 |
安定剤、顔料 |
Pb、Cd、Cr+6 |
塗料、インク |
顔料、着色料 |
Pb、Cd、Cr+6 |
めっき |
防錆、光沢剤 |
Cd、Cr+6 |
電子部品、はんだ |
リードめっき |
Pb |
日本版RoHS(J-MOSS)とは
J-MOSSとは、資源有効利用促進法に基づき環境配慮設計をJIS化(JIS C 0950)したもので、いわゆる電気・電子機器の特定化学物質の含有表示を義務化したものです。
J-Moss:The marking for presence of the specific chemical substances for electrical and electronic equipment
RoHS指令とJ-MOSSの違いを下表に示します。
|
RoHS指令 |
J-MOSS(日本版RoHS) |
---|---|---|
対象製品 |
ほとんど全ての電気電子機器が対象。ただし、医療器具および制御器具は除く。 |
テレビ、エアコン、冷蔵庫、洗濯機、パソコン、電子レンジ、衣料乾燥機の7品目 |
対象物質規制方法 |
6物質の使用制限(原則禁止) 2019年7月よりフタル酸類の4物質(DEHP、BBP、DBP、DIBP)が追加される予定 |
基準値を超えて6物質が含まれる場合は、含有マークと情報公開の義務化(グルーンマークは任意) |
適用時点での対応 |
2006年7月1日 上市する対象製品の非含有 |
2006年7月1日以降に製造・輸入・販売された対象製品が該当 |
製品等の入出庫管理(倉庫の管理)
倉庫業務担当者の基本は、正確な入出庫管理です。以下に、倉庫業務についての基本的な事項を示す。
倉庫の機能及び倉庫業務の基本
倉庫の機能は、
- 物(原材料、部品、半製品、製品)を保管すること
- 物を適切に出し入れすること
であるため、
倉庫業務の基本は、以下のことになります。
- 正確に決められた場所に入庫すること
- 正しい物を素早く探し出庫すること
近年、IT端末利用等で合理化が進んでいますが、倉庫業務担当者として、自分でどこにどの製品があるかを頭に入れておくことは変わらず有効です。
この際の着眼点として、類似製品(形状、品番等)、入出庫の頻度、長期滞留品などが挙げられます。
倉庫業務管理の基本「棚札」
倉庫業務管理の基本は、「棚札」にあります。
倉庫業務には正確な入出庫が求められますが、その履歴を管理することも重要です。
どの程度の頻度で動いているのか、残量はどのぐらいかというのは大切な経営データでもあるため、保管している品物ごとにその履歴がすぐに分かるようにしておくことが大切です。
保管している品物の履歴が分かるものは、「棚札」と呼ばれ、入庫や出庫により在庫の数に動きがある毎に「棚札」に記録します。
手書きであれ端末管理であれ、棚札に正確な情報が反映されるようにすることも倉庫業務の大切な仕事の1つです。
倉庫業務の最重要事項「現物管理」
倉庫業務の最重要事項は、「現物管理」です。
正確に素早く入出庫を行い、そのデータを正確に棚札に反映すると共に、最も大切なことは倉庫にある物(現物)を管理することです。
この「現物管理」には、次に示す様に切り口が2つあります。
- 棚札の情報と一致する在庫数が本当にあるかどうか確認すること
- その品物がダメージを受けて不良品になっていないかなど状態を確認すること
倉庫業務担当者は、データを追うだけでなく、常に現物の状態を把握することも大切な業務です。
倉庫業務の注意点
(1)先入れ先出し
先に仕入れたものを先に出庫し、長期滞留による保管物品の品質劣化を防ぐ在庫管理方法
(2)類似製品(製品形状、外箱のサイズ等)の入庫においては、パレットを分ける、保管場所を離して保管する等して、ピッキング時の誤りを防止する。
在庫管理の問題は複合問題
在庫数量に関する問題(在庫の数量が合わない)
在庫管理により発生する問題には、棚卸しの際に在庫の数量が合わない、在庫データが不正確である、工程内での在庫数が不正確であるといった問題があります。
在庫管理の8個の問題と原因
在庫の問題には、以下のような原因が多い。
(1)5Sによる問題
- 物の置き場所が決まっていない。
- 決まっていても守られていない。
- 作業員の判断で適当な場所に置いてしまう。
結果、在庫確認時に漏れが生じる。
(2)表示用紙のフォーマットの問題
製品名、ロット番号、数量などを記載している表示用紙(棚札等)の数量記載の箇所が小さすぎて、記入した数字が見難い。
(3)表示用紙の貼り位置の問題
- 表示用紙を製品箱に付ける位置のルールがない。
- 作業員の判断で付けているため見づらい。
- テープで表示用紙を留めているため途中で紛失する。
- 1箱1枚の原則を守らず複数枚付けてしまう。
(4)表示用紙の管理の問題
- 記入すべき項目に何も書いていない。
- 数字を下手な字で書いている(改訂ある数字が7なのか1なのか分からない等)。
- 間違えた数字を線で消した上に書き直している。
(5)数量管理の問題
- 製品箱に入っている製品の数量が表示用紙の数量と合わない。
- 不良品や抜き取りなどで減った数量を記入していない。
- 実数を数える箇所で数えておらず、表示用紙の数字を使い計算している。
- 実数を数える際に紙の切れ端に数字を書いているため、間違えやすい。
- 数字の計算時に検算しないため、計算間違いの数字を記入する。
- パソコン入力の際に入力間違いをする。
(6)ルールの問題
- 在庫数量を一斉に調べる際の時間が不明確、不徹底なため数字の重複や消滅が発生する。
- 在庫確認の時間に払い出しや受け取りが行われるため、不正確な数字となる。
- 在庫をどの順番で確認するかのルールが不明確である。
- ロット不合格や特別な検査などで製品が正規のルート以外に移動した際の在庫確認のルールがない。
(7)情報ルールの問題
- 在庫を確認する、在庫を集計する、集計したデータを配布するなどの情報のルール(時間、担当者、連絡方法など)が不明確である。
- 情報のルールは明確であるがコミュニケーションが悪いため守られていない。
- 欠勤者がいるとルールに混乱が生じる。
- 在庫異常の有無の検証ルールがないため、在庫の異常が分からない。
(8)コミュニケーションの問題
- 在庫管理に関わる担当者同士の人間関係が悪く、情報を伝えない。
- 緊急時なのに連絡せず「相手が聞きに来ないので連絡しなかった」などの言い訳をする。
- 相手に直接言うのが嫌なのでメールを使う、部下同士で連絡させるため誤解や時間のずれが生じる。
在庫問題(複合問題)の解決の進め方
一般的に在庫の問題は単純にシステムの問題だけと思われがちです。そのため「ちゃんと表示をするように」、「確実に勘定するように(数えるように)」などの指示になりがちです。
しかし、実際には、お互いに連絡しない、アドバイスしないなどの問題が潜んでいることが多いのです。
在庫問題には複合的な問題が絡んでいるケースが多いので、現場で現物を見て、担当者から徹底したヒアリングを行い、真の原因を探ることが大事です。
まとめ
ここでは、「品質マニュアル3.0」の関連規定の1つ「製造管理規定」を補足する「製造管理の参考」のうち「製造の品質」についての補足について、以下の項目でまとめました。
- 品質管理の心構え「次工程はお客様」とは
- 変化点管理(4M変更管理、3H管理)による事故やトラブルの防止
- 製品の3要素(QCD)と製造の4M
- 4M変更における変化点
- 自社内及び外注先の変更点管理における注意事項
- 3H管理
- 異常管理
- 「異常」とは
- 異常時の役割(作業者、現場リーダー)
- 4M変更管理
- RoHS指令/ELV指令について
- RoHS指令/ELV指令
- 日本版RoHS(J-MOSS)とは
- 製品等の入出庫管理(倉庫の管理)
- 倉庫の機能及び倉庫業務の基本
- 倉庫業務管理の基本「棚札」
- 倉庫業務の最重要事項「現物管理」
- 倉庫業務の注意点
- 在庫管理の問題は複合問題
- 在庫数量に関する問題(在庫の数量が合わない)
- 在庫管理の8個の問題と原因
- 在庫問題(複合問題)の解決の進め方