「品質マニュアル3.0」の関連規定の1つ、「製造管理規定」に関連する製造管理の参考のうち「製造の分析・評価・改善」についての補足資料です。
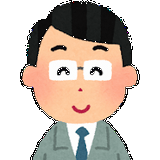
製造はしているが仕組みとして明確になっていない場合などに考慮すべき内容を含めています。
改善とQCストーリー
QCストーリー
改善とは、「経営システム全体、又はその部分を常に見直し、能力の向上を図る活動」となり、改善活動とも言われている。
この改善という言葉は、海外ではKAIZENと書かれ、日本で進化・発展した品質管理における大切な活動となっている。
改善活動は、現状の作業における問題(あるべき姿と現状とのギャップ)を発見し、その原因を取り除き、より良い作業の状態を生み出す活動ともいえる。
問題解決手順を活用して改善を進める代表的な手順として、以下にQCストーリーの1例を示す。
QCストーリーは単に一連の手順(ステップ)をこなすだけではなく、例えば、「効果の確認」の段階で効果が不十分で目標を達成していないときは、それ以前の段階、時には計画からやり直す活動を繰り返します。
品質や工程、仕事などの改善活動を繰り返し持続的に行うことが大切です。(継続的改善)
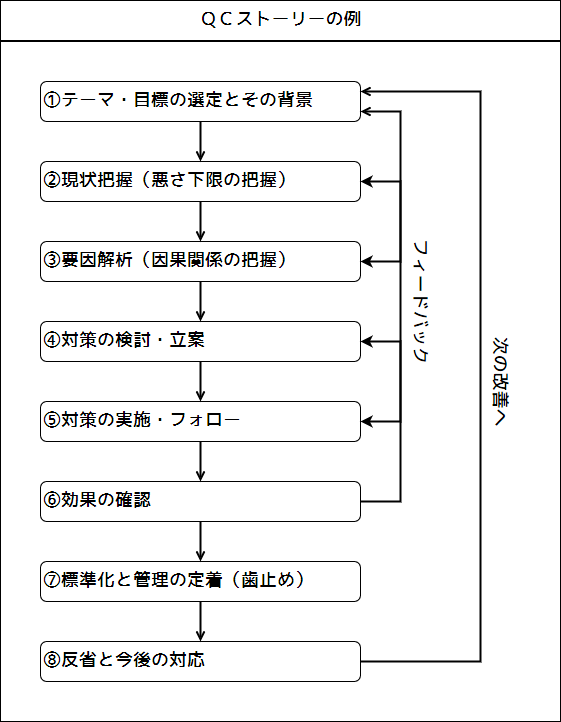
QCストーリーの例
また広い意味で、改善には、問題解決だけでなく、ありたい姿(目標)とのギャップを解消する課題達成の活動もあり、これを進める手順として課題達成型QCストーリーも別途提唱されています。
なお、QCストーリーの手順は、必ずしも一つの型に固定されたものではなく、改善の対象・範囲などにより、ステップの修正や新しい改善の手順がさまざまに創意・工夫されている。
小集団改善活動(QCサークル活動)
改善活動を進める場合、職場の仲間同士で小グループを作り、職場の改善を進めていくことがあり、小集団改善活動と呼ばれる。
日本では、活動の運営を自主的に進めていくことを基本に、職場の改善だけでなく、勉強することによる力量の向上や職場の活性化、さらには仕事のやりがいなどを目指したQCサークル活動と呼ばれる小集団改善活動が有名である。
このQCサークル活動は海外でも注目され、QCサークル活動が行われている。
作業標準
作業標準とは
作業標準とは、「作業条件、作業方法、管理方法、使用材料、使用設備その他の注意事項等に関する基準を定めたもの」であり、良い品質の製品を安く、早く、作ることを目的とした「重点作業を見る管理ツール」とも言われる。
品質工程図、検査規格も作業標準の一部である。
作業標準の内容
作業標準は、作業者が使用するものであり、曖昧な表現は避け、理解しやすいように工夫して作成することが重要である。
作業標準には、次の事項を規定して明記する。
- 使用材料・部品、使用設備
- 品質基準
- 作業手順・方法、作業上の注意事項
- 管理項目と管理方法、品質特性と検査方法
- 起こりやすい異常と処置の方法
- 作成と改定履歴
生産活動(製造)の標準化とPDCA
現場管理において生産活動を標準化することは重要なことである。
「標準化」と「PDCA」が生産活動における品質管理の2大要素である。
標準化とは、生産活動における重要なポイントである。
標準化 |
Standardization (スタンダード) |
標準を定め、活用する。 品質をそろえる。 |
---|---|---|
単純化 |
Simplification (シンプル) |
使用の統一・整理 品種の減少・共通化 |
専門化 |
Specialization (スペシャル) |
生産活動の集中 効率化・分業化 |
P(Plan) |
計画を立てる |
---|---|
D(Do) |
計画に沿って実施する |
C(Check) |
実施計画を確認する |
A(Action) |
確認結果に対して、適切な処置をする |
標準化の特色と位置づけを以下に示す。
・標準化が土台となってPDCAの水準が向上する。
・標準化がないとPDCAが崩れてしまう。
製品の標準化 |
|
---|---|
管理の標準化 |
|
やってはいけない「3S」とは
製造業でやってはいけない「3S」は工場での問題・課題を見つける切り口としてだけでなく、経営上大切なキーワードです。
- 先送り(Sakiokuri:サキオクリ)
- 仕損(Shison:シソン)
- 仕掛り(Shikakari:シカカリ)
先送り(問題の対策の先送り)
現場では、日々さまざまな問題が発生しています。
問題の対策の先送りなど、意思決定をせずに問題を放置しておくことは、問題を肥大化させ、問題の根本的な解決を遅らせてしまいます。
製品の品質を高める上で、意思決定にもとづき、現場で適切な行動をすばやくとることが大切です。
仕損(工程不良品)
現場で発生する仕損は、工程不良品です。
工程不良品の発生は、製品の原価を押し上げ、工程内の生産効率を低下させ、より多くの稼働時間がムダに消費されることになります。
購入した不良部品をくみこむことで発生する部材起因不良や自社の加工で発生した加工起因不良など、仕損が発生しないような事前の部材メーカーへの品質管理や自社の工程品質のつくりこみが大切です。
仕損の発生ポイントとして、三ム(ムリ、ムダ、ムラ)に着目して、改善します。
例)ムリ
ムリな作業、ムリな置き場 など
例)ムダ
ムダなうごき、ムダな仕掛品 など
例)ムラ
ムラのある動き、ムラのある教育、ムラのあるデータ など
仕掛り(つくりかけの製品)
仕掛りは、加工工程途中のつくりかけの製品のことです。
製造業での製品でも、新鮮な「生もの」だとおもって、途中で仕掛品として、滞留させずに、鮮度を保てるように生産できるように生産バランスを管理することが大切です。
工程中で仕掛品が発生しているということは、全体の工程の生産速度のバランスが崩れていて、生産速度が速い工程でムダに多く作り、遅い工程の前でたまっていることになります。
工程内では仕掛品がたまることで、保管場所も膨らみ、一部のボトルネック工程ではフル生産対応をせざるをえない状態になります。
このような場合は、製造工程では、下記のような取り組みが必要です。
- ボトルネック工程に合わせて、他工程の生産を調整する。
- ボトルネック工程自身の生産効率をUPさせて、生産性を向上させる。
- 仕掛品の色別管理、識別管理、置き場管理を明確にしてムダを削減する。
さらに、類似の製品を厚みの違いなどでお客様の要望にあわせて、多種類生産するなどの対応が求められる場合など、お客様からの発注情報にもとづく綿密な生産計画の立案で、ムリな生産にならないような事前の調整が必要です。
営業と製造との打合せ、変更に関わる連絡などの密な連携が必要になります。
製造品質:QC7つ道具
品質管理では、事実に基づいて、問題の状況を把握し、プロセス(工程)の良し悪しを判断し、PDCAを回しながら改善活動を行う。この際、事実とデータで話をすることが重要である。
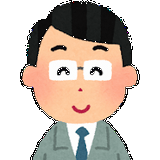
その人にどのような知識や経験があろうとも、「○○さんが言ったから」では、残念ながら伝わらないし残らないようです。
品質管理に使われる手法(QC手法)は、統計的手法とも言われ、事実とデータを分析する手法であり、たくさんの種類がある。実際に品質管理、品質改善するときに多く使用されている手法は、次に示す7つの手法で、「QC7つ道具」と呼ばれている。
分析・評価を行う上で最も大切なことは、問題解決、又は課題達成のために、ツール(QC7つ道具)を活用してデータを収集・分析し、そこに示されている情報をしっかり読み取ることであり、得られた図や表から「何が言えるか」を考え、意見をまとめる。
特に、何らかの目的をもって収集したデータについては、その目的からみて「何が判ったか」を考察するとともに、「次に何をすべきか」を検討し、次のアクション(行動)につなげていくことが重要であり、プロセスの情報を正しくつかみ、「プロセスに対して何をするか」を具体的に考え、次の行動につなげる必要がある。
1 |
特性要因図 |
仕事の結果(特性)に対する原因(要因)を整理する。 ・品質特性に影響を与えている要因を探すのに役に立つ |
---|---|---|
2 |
管理図 |
工程が安定状態で維持管理されているか判断するための図 |
3 |
グラフ |
データの時間的変化や項目別の比較などを図的に見る。 ・データを一見して、誰にでもよく判るようにできる |
4 |
チェックシート |
チェックするだけで簡単に結果が分かる表や図 ・目的に合ったデータを簡単に取れ、確認の抜けも防止できる |
5 |
パレート図 |
問題点を見出し、重点指向(改善の優先順位)を可能にする。 ・最も重要な問題や原因を客観的に知ることができる。 |
6 |
ヒストグラム |
ばらつくデータの分布の特徴をつかむ。 ・取得したデータ(測定値)の全体の分布が見やすい。 |
7 |
散布図 |
対になった2種類のデータの関係を見つける。 ・「結果と原因」、「特性と特性」、「要因と要因」の関係を見る場合に使う。 |
製造現場での異常を早期発見するための管理図活用
グラフと管理図の違い
日々のデータを記録したグラフは管理図と似ているが、グラフは製品規格線で結果を見ており、不良品が出る前に工程の異常を見つけることは難しい。そこで多くの製造現場で管理図が使われている。
下表にグラフと管理図の違いを示す。
|
グラフ |
管理図 |
---|---|---|
目的 |
見える化 |
ばらつきによる異常を発見 |
内容 |
不良率などの結果など |
品質要因など |
分かる事項 |
規格線に基づき製品の合否判断 |
管理限界線データの分布に基づき工程の異常を診断 |
管理図は工程が安定した状態にあるかどうかを調べるため、あるいは工程を安定した管理状態に保つために用いる管理限界線を入れた図です。
管理図は工程の異常を見つけるツールであり、現場が書くものであり、まず、現場がその必要性を認識することが大切です。管理図の作成には少し負担がかかりますが、しっかりした工程管理が確立されることで、結果的には現場のメリットにつながります。
主な管理図の使い方
管理図は、プロセス(工程)異常の検出を目的として、時間の経過とともにプロセスの変動や傾向の状態を視覚化するために用いられ、プロセスからデータをとり、それを折れ線グラフに表します。
管理図には、データから計算して得られる中心線(CL:Central Line)と上側(上方)管理限界線(UCL:Upper Control Limit)、下側(下方)管理限界線(LCL:Lower Control Limit)の3本の管理線が引かれ、上限管理限界線(UCL)と下限管理限界線(LCL)という2本の線によって管理します。
基本的には、管理図にプロットされた測定データがこの範囲(2本の限界線の中)に入っていれば、工程は安定した良い状態で維持、管理されていると判断します。打点が管理限界線から飛び出たり、中心線の上側又は下側に連続して偏って打点されたりする等のくせがあるときには、工程に何らかの異常があると考え、要因分析、対策立案のステップで問題を解決していきます。
管理図の見方と異常の見つけ方
「工程が安定状態になる」と判断する基準は次の通りです。
- プロットした点(データ)が管理限界線の外に出ない。
- プロットした点(データ)の並び方にくせがない
プロットした点(データ)が管理限界線内であっても異常であるケースを以下に示します。
- 毎週月曜日が悪いなどデータに周期がある。
- 連(中心線の片側に7点以上の打点が続く)がある。
- 7点以上の上昇、下降傾向がある。
- データの分布に2つ以上の山がある。
- 限界線付近に頻繁に点があらわれる。
管理図で何を管理するか
管理図は工程を管理するために使用するもので、管理特性として不良率や製品規格になっている特性を選ぶ必要はありません。すなわち、不良品の因果関係を明確にし、不良品に対し最も影響の強い要因を管理することが大切です。
管理図を使った工程解析、工程管理の手順
管理図を使い工程解析、工程管理を進める手順を示します。
【工程解析の場合】
- 管理特性を選定する(技術的に重要な特性、数値化しやすい特性など)
- 管理図を選定する(管理特性に応じて、適切な管理図を選ぶ)
- サンプリングのやり方を決める(サンプルの大きさ、サンプリングの時間間隔など)
- データを取り、管理図にプロットする
- 管理図により工程の安定状態を解析し、工程改善を行う
- 規格値と照合して、工程能力を調べる
【工程管理の場合】
- 管理限界を設定する
- データを取り、管理図にプロットする
- 異常が検出されたら、原因を究明して処置をする
- 管理限界値を再計算し更新する。上限管理限界線(UCL)と下限管理限界線(LCL)の再設定
なお、次のような場合には管理限界値を更新します。
- 工程に技術的あるいは設備的に明らかな変更があった場合
- 管理図に異常が現れて、工程が変わったことがはっきりした場合
- 工程に変更がなくても、一定期間経過した場合
参考資料
参考資料として、まずは、品質管理検定(QC検定)「4級用テキスト(4級の手引き)」をおすすめします。
工程能力とは
工程の品質的能力を表す指標として、工程能力指数による評価方法がある。
工程能力とは、与えられた標準通りの作業が行われた時、どの程度の品質が実現するかを示すものであり、決められた作業条件のもとで製造された品質のバラツキを評価することが重要である。
生産準備段階で調査した品質特性のバラつきが規格を満たしても、実際の製造段階(量産段階)と異なる製造をした場合(例えば十分な注意と念を入れた作り方をした場合)のバラツキでは、実際の製造段階(量産段階)で再現できない。
工程能力を常に良い状態に保つことは、製品の品質保証の基本でもある。
例えば、旋盤加工なら刃具の摩耗をも考慮して、どの程度のバラツキを生じるのか、そのバラツキと規格の幅とは比較して、十分な能力なのかどうかの検討が必要となる。
取得したデータをグラフ化して、特に顕著な傾向やクセ、あるいは異常値が見られないことだけでなく、規格に対して「ゆとり」をもったバラツキをしていることが重要です。
工程能力調査結果の判定基準を下表に示す。
工程能力不足の場合、工程能力指数は小さい値を示す。
工程能力指数 の判定基準 |
判定 |
不良品の出る確率 |
備考 |
---|---|---|---|
Cp≧1.67 |
工程能力は非常にある |
0.6ppm(0.00006%)以下 |
自動車部品など 無検査可 |
1.33<Cp<1.67 |
工程能力は十分にある |
0.6~60ppm (0.00006~0.006%) |
電気部品など 管理検査あるいは無検査可 |
1.00≦Cp≦1.33 |
工程能力は十分とは言えないがまずまずである |
60ppm(0.006%)~0.3% |
抜取検査あるいは管理検査 |
Cp<1.00 |
工程能力は不足している |
0.3%以上 |
全数検査が必要 品質改善要 |
注1)Cpは、バラツキを判断する。
注2)Cpkバラツキ、偏りの両方を判断する(Cpと同様の基準)
「工程能力指数(Cp)」とは、「ある品質特性において規格幅を6σ(±3σの幅)」で割った値」で定義されます。
なお、ここでいう工程能力とは、「規格に対する工程のバラツキの大きさ」を示す能力のことで、工程の生産量、能率を表す能力とは異なる。
FMEA(故障モードと影響解析)とFTA(故障の木分析)
FMEAとFTAは不良を予防する手法の1つで、品質改善活動においてよく使われている手法である。
FMEAとFTAの結果は、品質工程図、検査規格に盛り込む。
FMEA(Failure Mode and Effects Analysis)
故障モードと影響解析
FTA(Fault Tree Analysis)
故障の木分析
FMEA |
Failure Mode and Effects Analysis(故障モードと影響解析) ・事前に故障モードを予想してその影響を評価し、事前に対策処置をする方法 ・FMEAには、「設計FMEA」と「工程FMEA」の2つがある。 ・製造現場では、工程FMEAが主流 |
---|---|
FTA |
Fault Tree Analysis(故障の木分析) ・事前に望ましくない事象を出発点に、その発生原因を遡って根本原因を特定+影響度の大きいものから改善することにより、事象発生の未然防止を図る手法 ・生産の4Mと管理方法にフィードバックできる |
|
特長 |
活動内容 |
備考 |
---|---|---|---|
FMEA |
部品又は単位工程での不良 システム全体の影響を事前予測 |
①不良モードを予測する 過去の不具合事例も参考とする ②予測結果から、製品への影響度合を評価する ③予測結果の原因を考え、対策処置する |
想定・予測される不良モードに対して、その影響度を事前に評価し、原因を追究し、対応処置すること |
FTA |
想定不良に対する予防的改善活動 |
①不良(望ましくない事象)を解析する ②原因を究明する ③原因を排除する (対策の効果確認) ④さらに、水平展開する |
発生した不良に対して、その原因を追究し、生産の4M及び管理面から対応処置すること |
まとめ
ここでは、「品質マニュアル3.0」の関連規定の1つ「製造管理規定」を補足する「製造管理の参考」のうち「製造の分析・評価・改善」についての補足についてまとめました。