ISO9100:2016版対応の「QM-9100版品質マニュアル」の関連規定の1つ、「製造管理規定(QM9100版)」の一例です。
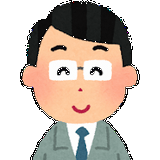
製造はしているが仕組みとして明確になっていない場合に考慮すべき内容を含めています。工場長入門のイメージでまとめています。
製造管理や安全衛生管理についての参考資料は、最後にまとめまています。
- 1. 目的
- 2. 適用範囲及び関連法規等
- 3. 関連規定等及び製造に関する用語の定義等
- 4. 製造プロセスの手順と記録
- 4.1 製造プロセスの管理状態
- 4.1.1 文書化した情報の利用
- 4.1.2 監視及び測定のための資源
- 4.1.3 監視及び測定
- 4.1.4 インフラストラクチャ及び環境
- 4.1.5 要員の力量
- 4.1.6 妥当性確認及び特殊工程
- 4.1.7 ヒューマンエラーの防止
- 4.1.8 リリース(出荷)及びアフターサービス
- 4.1.9 作業のできばえ
- 4.1.10 製造中の製品の状態把握
- 4.1.11 クリティカルアイテムの管理及び監視
- 4.1.12 ばらつきの測定方法
- 4.1.13 後工程で十分な検証ができない場合の対応
- 4.1.14 製造及び検査・検証作業の証拠
- 4.1.15 異物混入防止、検査及び除去
- 4.1.16 ユーティリティ及び供給物の管理及び監視
- 4.1.17 回収及び交換
- 4.2 設備、治工具及びソフトウェアプログラムの管理
- 4.3 特殊工程の妥当性確認及び管理
- 4.4 製造工程の検証
- 4.5 製造プロセス
- 4.1 製造プロセスの管理状態
- 5. 製造
- 6. 製造についての分析・評価・改善
- 7. 製造工程の変更管理
- 8. 識別及びトレーサビリティ
- 9. 顧客や外注・購買先から預かるもの(顧客支給品)の管理
- 10. 製造工程の設計及び特殊工程の妥当性確認
- 11. 試作管理
- 12. 記録の管理
- 【参考】製造に関する参考資料
- まとめ
1. 目的
本規定は、当社における製造に係る手順等を定め、製造業務を効率的に運用することを目的とする。
2. 適用範囲及び関連法規等
本規定は、当社の製造業務(製品保管、入出荷管理を含む)に適用する。
3. 関連規定等及び製造に関する用語の定義等
3.1 関連規定等
(1)当社の安全衛生管理は、「安全衛生管理規定」に従い、安全衛生管理体制により実施する。
(2)外注・購買については、「外注・購買管理規定(QM9100版)」に従い実施する。
(3)製造に関する標準等
「製造設備等の管理」
3.2 製造に関する用語の定義等
本規定における用語の補足について、「製造管理規定の用語の補足説明」に示す。
3.3 本規定における製造組織
本規定における製造組織と主な業務を、以下に示す。
製造部 | 製造管理 | 購買、外注管理、製造計画、製品保管、入出荷(入出庫) |
---|---|---|
製造 | 製品製造、工程管理、工程内検査、設備管理 | |
検査 | 最終検査 |
3.4 製造業務を担当する部署長の役割と責任
(1)製造業務は、製造部が実施する。
(2)製造部長は、3Sに努め、報連相を徹底し、安全第一で製品品質を確保できるよう製造現場の環境を管理する。
(3)安全衛生管理
製造部長は、「安全衛生管理規定」に基づき製造部及び作業者の安全衛生を管理する。
- 作業環境の整備(危険防止)
- 安全又は衛生のための教育の実施
- 快適な職場環境の形成
(4)製品品質の確保
- 製造品質、入出庫・保管時の品質保持
(5)製造工程の管理
- 製造部長は、材料・部品等(製造委託先が製造する製品を含む)の受入、製造、製品の引渡しまでの各工程について管理する。
- 材料・部品等には、材料、部品、半製品を含む。
(6)製造設備等の管理
- 製造設備等の管理
- 製造部長は、以下の設備等について、「安全衛生管理規定」に従い保守管理を行う。
- 製造設備、製造に使用する装置等の監視機器(以下製造設備という)
- フォークリフト、天井クレーン
- 製造部長は、以下の設備等について、「安全衛生管理規定」に従い保守管理を行う。
- 監視・測定機器の管理
- 製造部長は、受入検査、製造、工程内検査、最終検査、試験などにおいて使用される監視・測定機器について、「監視・測定機器管理規定(QM9100版)」に従い管理する。
- 有機溶剤等の管理
- 製造部長は、有機溶剤等について、「安全衛生管理規定」に従い管理する。
(7)在庫管理(製品の保管、入・出荷管理)、実地棚卸
- 実地棚卸では、在庫と基幹システムと差異を確認する。
- 製造部長は、実地棚卸の実施要領を定め実施する。
(8)教育・訓練
- 「教育」とは知らないことを教えること、「訓練」とは繰り返し実践させてできるようにすることである。
- 作業者は「訓練」をしないと忘れてしまうため、製造部長及び現場リーダーは、作業者に対し継続的に「訓練」を行うと共に、訓練の仕組化(訓練記録、実施状況確認、スキル管理)も併せて行う。
(9)その他の業務
- 原価管理(常に原価を意識しながら製品を作り続けていくこと)
- 外注・購買(材料購入を含む)は、「外注・購買管理規定(QM9100版)」による。
- 納期管理
- その他製造に関する業務
4. 製造プロセスの手順と記録
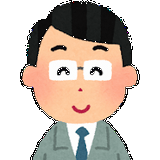
「4.1 製造プロセスの管理状態」の記載方法は、ひと工夫必要だと思います。
4.1 製造プロセスの管理状態
製造及びサービス提供において、管理された状態とは、以下の事項について該当するものを必ず含めた状態をいう。
4.1.1 文書化した情報の利用
次の事項を定めた文書化した情報を利用できるようにする。
1)製造する製品、提供するサービス、又は実施する活動の特性。
2)達成すべき結果
なお、文書化した情報について以下補足する。
- 製品及びサービスの特性を定める文書化した情報には、デジタル製品定義データ、図面、部品リスト、材料及び工程仕様書が含まれる場合がある。
- 実施する活動及び達成すべき結果についての文書化した情報には、製造工程表、管理計画、製造文書(例えば、製造計画書、トラベラー、ルーター、作業指示書、工程カード)及び 検証文書が含まれる場合がある。
4.1.2 監視及び測定のための資源
監視及び測定のための適切な資源を利用できるようにし、かつ、使用する。
4.1.3 監視及び測定
プロセス又はアウトプットの管理基準、並びに製品及びサービスの合否判定基準を満たしていることを検証するために、適切な段階で監視及び測定活動を実施する。
監視・測定には、以下の事項を含める
(1)製品及びサービスの合否判定のための監視及び測定活動について文書化した情報は、次の事項を含める。
- 合格及び不合格の基準
- 検証作業を実施すべき工程順序
- 保持(記録)すべき測定結果(最低限、合格又は不合格の表示)
- 要求される特定の監視及び測定機器、並びにそれらの使用に関連する指示書
(2)抜取検査を製品の合否判定の手段として使用する場合、抜取計画は認知された統計理論に基づき正当化されたものであり、使用に適するものであることを確実にする。
なお、「使用に適する」とは、抜取計画が製品の重要性及び工程能力に適していることである。
4.1.4 インフラストラクチャ及び環境
プロセスの運用のための適切なインフラストラクチャ及び環境を使用する。
例えば、品質工程図や作業手順書など、製造及びサービスの提供について定められたルールに基づきプロセスを実施する。
- 適切なインフラストラクチャには、製品の専用治工具(例えば、ジグ、固定具、型)及びソフトウェアプログラムが含まれる場合がある。
4.1.5 要員の力量
必要な適格性を含め、力量を備えた人々を任命する。
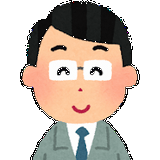
力量については、「教育・訓練規定(QM9100版)」に従い、製造部署で詳細を定めて運用すると分かりやすいと考えています。
4.1.6 妥当性確認及び特殊工程
以下の様なプロセスは、特殊工程と呼ばれる。
(参照:「QM-9100版品質マニュアル 8.5.1.2」)
製造及びサービス提供のプロセスで結果として生じるアウトプットを、それ以降の監視又は測定で検証することが不可能な場合には、製造及びサービス提供に関するプロセスの、計画した結果を達成する能力について妥当性確認を行う。
妥当性は、定期的に再確認する。
4.1.7 ヒューマンエラーの防止
ヒューマンエラーを防止するための処置を実施する。
4.1.8 リリース(出荷)及びアフターサービス
リリース、顧客への提供及び提供後の活動を実施する。
(参照:「QM-9100版品質マニュアル 8.6、8.5.5」)
4.1.9 作業のできばえ
「作業のできばえ」の基準を設定する。
「作業のできばえ」の基準には、規格書、標準見本、図解などがある。
4.1.10 製造中の製品の状態把握
製造中における全ての製品に関する状態を把握する。
把握する状態には、部品の数量、分割指示、不適合製品などがある。
4.1.11 クリティカルアイテムの管理及び監視
決められたプロセスに従った、キー特性を含む識別されたクリティカルアイテムを管理及び監視する。
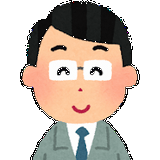
「キー特性」た「クリティカルアイテム」については、実務上具体的にどのようなことを意味するのか定めておくことが必要だと考えています。
4.1.12 ばらつきの測定方法
ばらつきの値を測定するための方法を決定する。
バラツキの測定方法には、治工具、機上測定プローブ、検査装置などがある。
4.1.13 後工程で十分な検証ができない場合の対応
後工程では適合について十分な検証ができない場合、工程内での検査・検証ポイントを明確にする。
4.1.14 製造及び検査・検証作業の証拠
全ての製造及び検査・検証作業が、計画のとおり又は文書化され、承認された他の方法のとおりに実施された証拠を利用できるようにする。
4.1.15 異物混入防止、検査及び除去
異物の混入防止、検出及び除去を規定する。
4.1.16 ユーティリティ及び供給物の管理及び監視
製品要求事項への適合に影響する範囲で、ユーティリティ及び供給物(例えば、水、圧縮空気、電気、化学製品)を管理及び監視する。
(参照「QM-9100版品質マニュアル 7.1.3」)
4.1.17 回収及び交換
後にその製品が要求事項を満たしていないと判明したときに回収及び交換ができるようにするため、後工程の製造で使用する目的で全ての要求される測定及び監視活動の完了前に、リリースされた製品であることを識別し、記録する。
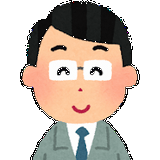
日本語が分かりにくいので、実務や現場で使われている言葉に合わせて意訳した方がよいと考えています。
4.2 設備、治工具及びソフトウェアプログラムの管理
製造工程を自動化、管理、監視又は測定するために使用される設備、治工具及びソフトウェアプログラムは、製造への最終リリース前に妥当性確認を行い、維持する。
保管中の製造設備又は治工具に対して、必要となる定期的な保存処置及び状態の点検を含む保管要求事項を定める。
4.3 特殊工程の妥当性確認及び管理
結果として生じるアウトプットが、それ以降の監視又は測定で検証することが不可能な場合のプロセスに対して、次の事項のうち該当するものについて含めた手続を確立する。
- プロセスのレビュー及び承認のための基準の決定
- 承認を維持するための条件の明確化
- 施設及び設備の承認
- 人々の適格性認定
- プロセスの実施及び監視に対する所定の方法及び手順の適用
- 保持すべき文書化した情報に対する要求事項
4.4 製造工程の検証
製造工程により、要求事項を満たす製品を製造できることを確実にするため、製造工程の検証活動を実施する。
これらの活動には、リスクアセスメント、生産能力(capacity)や製造能力(capability)の調査、及び、管理計画が含まれる場合がある。
製造工程、製造文書及び治工具により、要求事項を満たす部品及び組立品を製造できることを検証するため、新規の部品又は組立品の初回製造からの代表品を使用する。
この活動(初回製品検査(FAI))は、初回の結果を無効にする変更(例えば、設計の変更、製造工程の変更、治工具の変更)が生じたときには繰り返す。
製造工程検証の結果に関する文書化した情報を保持する。
4.5 製造プロセス
4.5.1 製造プロセスの基本フロー
製造プロセスの製造基本フローを下図に示す。
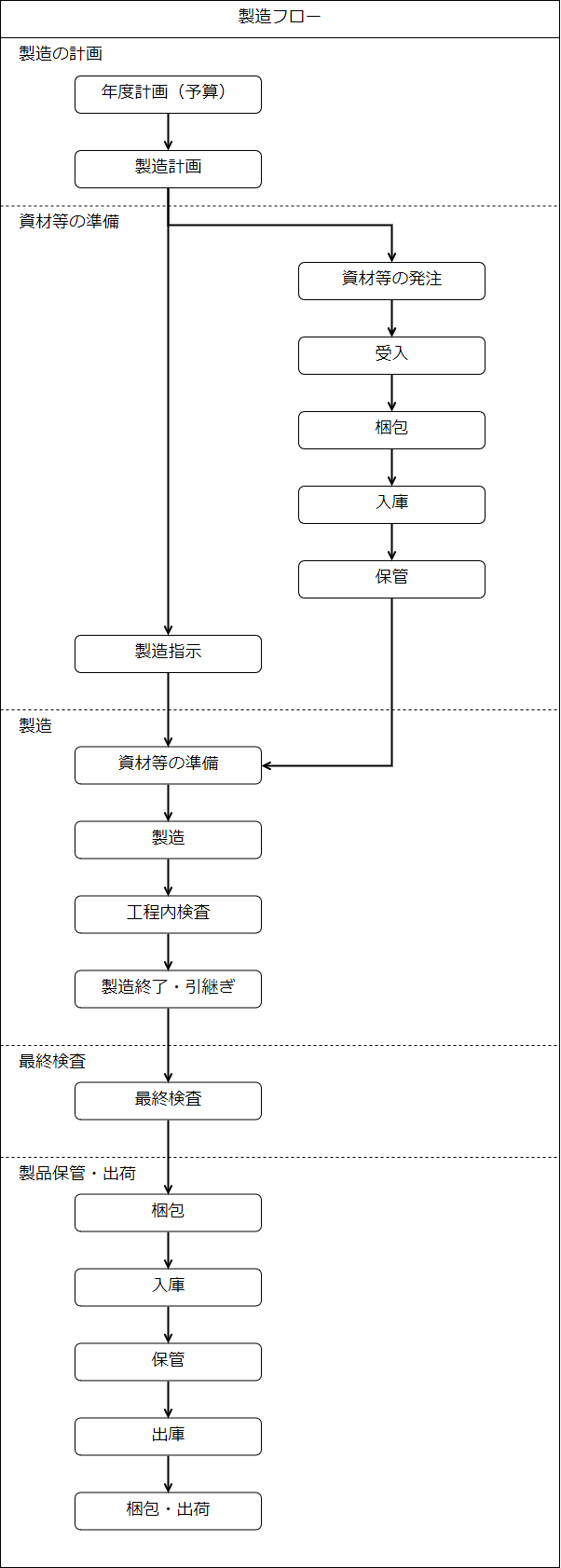
製造フロー
4.5.2 製造に関する主な管理事項と担当部署
製造に関する主な管理と担当部署について、下図に示す。
●:責任部署 ○:関係部署
|
製造部 |
管理 |
品証 |
||
---|---|---|---|---|---|
製造管理 |
製造 |
検査 |
|||
製品品質の確保、安全衛生等 |
● |
● |
○ |
|
|
作業環境の維持・改善、危険防止 |
● |
● |
○ |
● |
|
有機溶剤等の管理 |
● |
● |
|
|
|
製造設備、フォークリフト等の管理 |
● |
● |
|
● |
|
監視・測定機器の管理 |
● |
● |
● |
|
● |
製造関係の文書・記録の管理 |
● |
● |
|
|
|
5. 製造
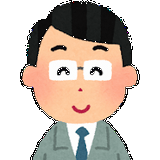
設備投資なども考慮して、3年程度の中期計画を前提とした年度計画にするのもよいと考えています。
5.1 製造計画
(1)年度の製造計画
- 毎期末の次期予算作成時に、年度の製造計画を作成する。
- 製造計画には、製造部で製造する製品の数量、生産予定、材料等を含める。
(2)毎月の製造計画
- 年度計画に基づき、実際の製造数を営業部と協議・決定する。
- 受注生産品や試作品の製造数量・日時について考慮する。
- 製造部は、営業部と協議した結果に基づき毎月の製造計画を立て生産する。
(3)製造の進捗管理
製造部は、製造実績を週次及び月次の実績をまとめて関係部署長に報告する。
5.2 材料・部品等、購買品及び支給品の受入
顧客等から支給される材料・部品等(支給品)の受入は、以下に示す材料・部品等及び購買品に準じて行う。
5.2.1 材料・部品等及び購買品の受入(入荷品の受入)
- 入荷品(納入品)は納品書に記載された品名、数量通りか確認する。
- 入荷品(納入品)は梱包表示等で管理する。
- 入庫処理については、「5.5.1 入庫」に示す。
(1)入荷品の情報(納期、購買先、品目名称、数量等)は、購買担当部署より入手する。
(2)納入品の受取
- 入庫担当者は、運送業者の伝票により入荷品の現物(品名、数量、破損の有無等)を確認し受け取る。
- 特に混載(1つのパレット、または、1つの箱・梱包に、2種類以上の製品・部品が含まれている場合)されている場合があるため、現物確認を徹底する。
- 入庫担当者は、入荷品を、決められた場所に保管する。
(3)入荷品の確認
- 入庫担当者は、入荷予定を参考にして、入荷品の品名、数量、梱包状態を確認し記録する。この際、現物確認を徹底する。
- 入荷予定にない入荷品については、購買担当者に確認する。
- 問題が発生した場合、購買担当者に連絡する。
(4)入庫担当者は、検査部署に検査を依頼する。
5.2.2 受入検査及び入庫(棚入)
- 入荷品(納入品)は「検査業務規定」基づき、受入検査を行い、合格・不合格を判定する。
- 検査結果は、スタンプ・札等で表示する。
- 入庫処理については、「5.5.1 入庫」に示す。
(1)受入検査合格品は、基幹システムに入力(在庫計上)し、棚入をする。入庫(棚入)日、数量等を棚札に記入する。
(2)受入検査不合格品は、不合格品置き場に移動する。不合格品の処置について購買に確認し、実施する。
(3)その日の入荷品について、購買に入荷品名、数量等を報告する。
5.2.3 入荷品の包装・保管
入荷品の包装・保管については、「5.5.2 包装・保管」に示す。
5.2.4 出庫(出荷)
(1)出荷明細を基幹システムから出力し、送り状を作成する。
(2)出荷明細に基づき、製品保管場所から製品等を取り出す。
- 製品を取り出す際、取り出した製品の品名、数量を確認し、出庫日及び出庫数量等を棚札に記入する。
- 取り出した製品を梱包場所に運ぶ。
(3)梱包
- 梱包する前に、出荷明細と取り出した製品の品名、数量等を確認する。
(4)決められた発送品置き場に置き、出荷する。
5.3 製造工程
5.3.1 作業指示(製造指示)
(1)製造計画による場合
- 製造管理部署は、製造部署に対し、「作業指示書」を発行し、製造を指示する。
- 製造計画に変更がある場合、製造部署に対しすみやかに連絡する。
(2)製造指示に変更があった場合
- 「作業指示書」発行後に、その内容に変更があった場合、すみやかに製造部署に変更を指示する。
- この際、「作業指示書」は、修正又は再発行する。
(3)緊急生産の場合
製造管理部署は、製造部署に対し、すみやかに緊急生産があることを連絡し、「作業指示書」により製造を指示する。
5.3.2 材料・部品等の準備
5.3.2.1 材料・部品等の購入
(1)使用する材料・部品等の新規及び追加購入
製造管理部署は、「製造計画」に基づき購買先から購入、受入、入庫する。
(2)使用する材料・部品等の払い出し
- 「作業指示書」に基づき製造管理部署から製造部署に払い出す。
- 製造部署は、製造に必要な材料・部品等を定位置に保管する。
- 材料・部品等の不足が予想される場合は、製造管理部署に材料・部品等の追加を依頼する。
(3)顧客支給品の管理
- 「作業指示書」に基づき製造管理部署から製造部署に払い出す。
- 営業からの依頼により、製造管理部署で受入後、入庫する。
5.3.2.2 材料・部品等の識別と管理
(1)材料・部品等の識別とトレーサビリティについて、「識別及びトレーサビリティ管理標準」に基づき以下について実施する。
- 購入、保管についての識別とトレーサビリティ
- 材料、部品、半製品の識別とトレーサビリティ
(2)材料・資材等は、2Sを徹底し、その品質を維持し、ロット、個数等を管理する。
5.3.2.3 製造に使用する工具等の管理
(1)製造に使用する工具等は、2Sを徹底し、管理する。
(2)工具等を使用する際は、使用前及び使用後の点検を行い、異常等があった場合には現場リーダーに報告し、日報等に記録する。
(3)使用中に工具等に異常があった場合には、直ちに作業を中断し、現場リーダーに報告し指示を待つ。
(4)製造設備の管理については、「3.4(6)」に示す。
5.3.3 製造(加工、組立等)
5.3.3.1 製造工程の管理
(1)製造時に使用する材料・資材等は、2Sを徹底し、その品質を維持し、ロット、個数等を管理する。
製造で発生した不適合品は、「不適合品処理規定」に基づき処理する。
手直しについても不適合品と同様の処置を取る。
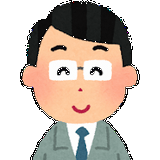
業種にもよるのでしょうが、「手直しゼロ」を追求するのか、ある程度の手直しを許容するのかは、社内(営業、調達、製造、品証)で共有されることが望ましいです。
さらに技術の設計にもフィードバックされると設計品質の改善にもルナがりよいと考えています。
(2)製造部長及び現場リーダーは、製品のQCD(品質・コスト・納期)を改善させ製品の競争力を高めるため、「品質を工程で作り込む」現場管理を進める。
(3)作業者は、製品の製造に当たり、「作業指示書」及び、図面、仕様書、品質工程図、作業手順書等に基づき実施する。
(4)製造部長及び現場リーダーは、製造及び製造に伴う作業に当たり、部下任せや現場任せにすることなく実態を確認し、自ら作業標準等を理解させ、作業手順書等のルールを順守させる。
(5)作業標準等のルールを守れない場合、製造部長及び現場リーダーは、関係者同士で「なぜ、ルールを守れないか?」を関係者と協議し対応を計画的に進める。
(6)製造に当たり使用する設備等は、「安全衛生管理規定」に従い使用する。
5.3.3.2 作業手順の変更時の対応
(1)当日の作業計画が変更になった場合
新しい作業指示書に基づき実施する。
(2)作業手順の変更の場合
納期変更等の理由により、作業手順(段取り)を変更する場合には、現場リーダーの指示を受けて実施する。
(3)作業手順書や品質工程図の見直しが必要な場合は、「7.1 工程の変更」による。
5.3.3.3 製造の進捗管理
(1)進捗管理の目的
進捗管理の目的は、納期の維持と生産速度の維持と調整である。
①納期の維持
納期を守ること。
②生産速度の維持と調整
納期を守るために製造を計画より先行して行うと、仕掛在庫が増加し原価を圧迫する。このため、生産リードタイムを考慮し、仕掛在庫を少なくするように適切な時期に生産する必要がある。
(2)進捗管理の流れ
進捗管理は、次に示す①~⑤の繰り返しである。
①ロット生産や流れ作業の進捗状態をつかむ。
②予定(計画)と実績との進みと遅れの差をチェックする。
③遅れが発生している場合は、スケジュールを調整する。
④遅れの原因を調査し、その対策を立案して実施する。
⑤遅れが回復したのを確認する。
(3)製造工程(プロセス)の進度管理(進捗管理)
- 製造の進捗管理は、製造計画及び「作業指示書」により行う。
- 製造部長は、製造が製造計画に対して計画通り進んでいるかを確認し、遅れている場合には対策し遅れを取り戻さなければならない。
5.3.3.4 異常時の対応及び処置(異常管理)
(1)製造部署の役割(異常管理)
- 現場リーダー及び作業者の役割は、要求されたQCD(品質、原価、納期)を満足する製品を製造するために、製造の4Mに気を配り、製造目標を達成することである。
- 現場リーダーは、作業者に、作業標準などで決められた作業を守り、計画された製造を完遂させるよう指導する。
- 現場リーダーは、担当する設備(あるいはライン)の状況を日頃からよく観察し、異常時には「どこが、どう違うか」を説明できるよう、継続的に指導をする。
(2)異常(不良やいつもと違うこと)発生時の原則
①製造部署長及び現場リーダーは、製造現場で異常(不良やいつもと違うこと)が発生した場合、直ちに現場に行き、現物を観て、現象を確認し、必要な処置・対策を取る。
②作業者は、製造現場で異常(不良やいつもと違うこと)が発生した場合、直ちに作業を中断し、現場リーダーを呼び、現場リーダーの指示を待つ。
(3)異常時の対応及び処置の流れ
①異常(不良やいつもと違うこと)の発見
異常に気付いた作業者は、ただちに作業を中断し、現場リーダーに報告する。
作業を中断した際、作業者は確実に安全処置を取る。
②異常の確認
現場リーダーは、現場、現実、現象を確認し、必要な処置を取ると共に、部署長及び関係者に連絡する。
③異常の原因調査と対応
製造部長及び製造部署長は、異常が発生又は発生の恐れがある場合、その原因を調査し、対策を取る。
異常により製造に遅れが生じる場合の対応例を下表に示す。
遅れの種類 |
原因 |
対策例 |
---|---|---|
計画に対して遅れている場合 |
遅れの原因を調べる。 |
明らかになった原因に対し部署内で対応する。 部署内で対応できない場合は、他部署を含め対策を検討する。 |
生産能力の不足による場合 |
注文の追加や飛び込み等による作業量の増加や作業者の欠勤などにより生産能力が不足する。 |
|
稼働率や作業能率の低下による場合 |
不良の発生、機械の故障、指示待ち、段取り、運搬などで稼働率が落ちる。 |
根本原因をつかんで対策を行う。 |
材料や部品の欠品による場合 |
材料や部品の納期遅れや発注ミスにより遅れが発生する。 |
外注先や購買先に督促や緊急発注をする。 発注のやり方を再考する。 |
(4)発生した異常及び対応等については、記録に残す。
5.3.4 工程内検査
(1)工程内検査員の資格
製造部長は、「教育・訓練規定(QM9100版)」に従い、工程内検査員に必要な教育・訓練を計画・実施し、必要な力量を持つと評価した作業者を、工程内検査員として登録した後、工程内検査を担当させることができる。
(2)工程内検査
製造工程において「品質工程図」等で指示された場合、工程内検査を行い所定の用紙に記録する。
監視・測定機器は、「監視・測定機器管理規定(QM9100版)」に従い、管理する。
(3)不適合品処理
製造工程において不適合品が発見された場合は、定められた場所又は指定の箱に隔離するものとし、「不適合品処理規定(QM9100版)」に従い、処理する。
5.3.5 作業終了時の業務(片付け、報告等)
製造担当者は、その日の作業終了後、以下について実施する。
①材料、部品、製品、及び作業場の整理・整頓・清掃を行う。
②その日の作業内容などを「日報」に記録し、報告する。
異常ではないが気づいた点、兆候、処置なども、日報に記録する。
③実施した製造記録等をまとめ、製造管理部署に提出する。
④製造記録等は、「品質文書管理規定(QM9100版)」に従い管理する。
5.4 最終検査
(1)製造終了後、製造部署は、作業指示書に対する出来高を記録し、製造ロットに対応する帳票を発行し、検査部署に検査を依頼する。
(2)最終検査に合格したロットは、生産実績の記録と共に製造管理部署に引渡す。
5.5 製品の入庫(入荷)・包装・保管(在庫管理)・出庫(出荷)
5.5.1 入庫
(1)製造管理部署は、最終検査に合格したロットを、生産実績の記録と共に引き受け、梱包・保管する。
(2)合格品の在庫計上及び入庫
製造管理部署は、合格品を基幹システムに入力し、在庫計上した後、入庫する。
(3)購買品の在庫計上及び入庫
製造管理部署は、購買品について、受入検査実施後、基幹システムに入力し在庫計上した後、入庫する。
(3)入庫時には、保管場所に設置されている棚札に数量等を記録する。
5.5.2 包装・保管
製造管理部署は、材料、製品、半製品及び仕掛品について、納入先への引渡しまでの間、保存・管理する。
(1)識別
材料、部品、半製品、製品の識別は、次のいずれか、又は、すべての方法で行う。
- 品名、納入先等を表記した荷札、ラベル等
- 専用の棚、場所など
- 立札
(2)取扱い
材料、部品、半製品、製品の移動、積み上げなどの際には、損傷・劣化のないように取扱う。
(3)包装
- 包装は、損傷、劣化を防ぐよう、「包装設計基準」により行う。顧客の指定がある場合はそれに従う。
- 輸送中又は引渡し後の取扱い時の損傷、劣化を防ぐため、必要に応じて注意事項を表示する。
(4)保管
- 材料、部品、半製品、製品は、指定された場所に保管する。
- 指定された場所には棚札を付け、入出庫に伴う在庫数等を管理する。
- 端数梱包箱には、表示等で全数梱包箱と識別する。
- 製品等の入出庫は定められた方法で管理する。
- 製品の損傷・劣化を防ぐため、緩衝材・乾燥剤などの処置を行う。
- 製造から3年経過した長期保管製品については、品質の確認、必要に応じ再検査を行う。(「検査業務規定(QM9100版)」参照)
- 棚卸については、「5.6 棚卸」に示す。
(5)保管(保存)に関するその他の要求
材料、部品、半製品、製品の保存の際、該当するものについては、仕様書及び適用される法令・規制要求事項に従い、次の事項も含める。
- 洗浄
- 異物の混入防止、検出及び除去
- 取扱注意を要する製品に対する特別な取扱い及び保管
- 安全警告及び注意を含むマーキング及びラベルの貼付
- 有効保管寿命の管理及び在庫品の回転
- 危険性のある材料の特別な取扱い及び保管
5.5.3 出荷
出荷業務は基幹システムを用い、以下の手順で実施する。
(1)出荷は、出荷予定に基づき出荷する。
(2)外注への支給は、指示書により行う。
(3)材料・部品・半製品は、振替を行う。
(4)当日出荷は、その日の12時迄に登録されたものを対象とする。
5.6 アフターサービス
5.6.1 アフターサービスの程度
製品及びサービスに関連するアフターサービスの程度(どこまでやるか)は、次の事項を考慮して決める。
なお、引渡し後に問題が検出された場合、調査及び報告を含む適切な処置をとる。
- 法令・規制要求事項
- 製品及びサービスに関連して起こり得る望ましくない結果
- 製品及びサービスの性質、用途及び意図した耐用期間
- 顧客要求事項
- 顧客からのフィードバック
- 運用データの収集及び分析(例えば、パフォーマンス、信頼性、教訓(lessons learned)など)
- 製品の使用、保守(整備)、修理及びオーバーホールに関連する技術文書の管理、更新及び提供
- 組織の外部で行う作業に対する必要な管理(例えば、組織の施設以外の場所での作業など)
- 製品・カスタマーサポート(例えば、問合せ、訓練、保証、保守(整備)、交換部品、資源、旧式化・枯渇(obsolescence)など)
5.6.2 返品の受入
返却品は、「営業業務規程(QM9100版)」に従い、営業部署の返品通知により受け入れる。
受入後の手順を以下に示す。
①製造部は、営業部署より返品通知を受ける。
②製造管理部署は、返品された製品を受領後、営業部に受領したことを連絡すると共に、品質保証部に検査を依頼する。
③品質保証部は、検査結果を製造管理部署に連絡する。
④製造管理部署は、当該営業部署に検査結果を連絡する。
不適合品(検査不合格品)は、「不適合品処理規定(QM9100版)」により処理する。
⑤検査結果で合格となった返却品については、製造管理部署は、返品通知に基づき、基幹システムに入力し在庫計上した後、入庫する。
5.6.3 製品の保守点検
出荷後に保守点検が必要となる場合の手順について以下に示す。
①点検を依頼する営業は、検査部署に依頼する。
②検査部署は必要な点検を行い、結果を記録する。
③点検終了後、当該営業に連絡し、出荷する。
5.7 棚卸(実地棚卸)
製造部長は、棚卸を実施する。
6. 製造についての分析・評価・改善
製造部長は、以下のデータを収集・分析・評価し、製造について継続的に改善すると共に、営業会議等で報告する。また、年間の分析・評価結果を次年度の計画に反映する。
製造についての主な分析・評価と担当部署について、下表に示す。
●:責任部署 ○:関係部署
|
製造部 |
購買 |
技術 |
品証 |
||
---|---|---|---|---|---|---|
製造管理 |
製造 |
品証 |
||||
データ収集・分析・評価 |
● |
○ |
○ |
● |
○ |
○ |
品質クレーム |
● |
○ |
○ |
● |
○ |
○ |
不適合品(製造部生産、外注品) |
● |
○ |
|
● |
○ |
|
製造設備稼働時間、材料ロス率等 |
● |
○ |
|
|
|
|
週報、月報、会議等で報告 |
● |
|
|
● |
|
|
6.1 分析・評価項目
(1)品質クレーム、不適合品(製造部生産品、外注品)
クレーム等発生原因、是正策、対策の有効性の評価
(2)製造プロセスのパフォーマンス評価
製造プロセスのパフォーマンス評価項目の例を次に示す。
- 製造設備の稼働時間、日数
- 製造に必要な材料の量、製品に使われた材料の量(材料のロス率)、製品数
- 製造開始までの準備時間、製造終了後の片付けの時間
(3)製造プロセスの改善
製造プロセスの改善指標の例を次に示す。
- 稼働率
製造設備の稼働時間/製造部稼働日数
- 生産性の例1
1人当たり労働生産性=生産量/作業者数
1時間当たり労働生産性=生産量/(作業者数×労働時間)
※労働時間:生産活動の時間、手直し等の時間は含まない。
- 生産性の例2
生産性=能力(能率)/効率
能力(能率)=生産数量/直接工数(時間)
効率=直接工数(時間)/全工数(時間)
※直接工数の指標としての時間の例
直接作業時間 |
生産に直接かかわる作業者達が実際に作業している時間の合計。工具の交換などの準備作業などの時間も含まれる。多くの製造部で有効。 |
---|---|
正味作業時間 |
製品を作る(直接付加価値を生む)作業時間の合計。準備作業などの時間は含まない。全業種で有効。 |
- 作業性
準備時間、片付け時間、段取り替え時間
(4)ロスコスト
クレームや不適合等により発生するロスコストの例を次に示す。
- 不適合品(廃棄品)の生産に要した工数(人工、設備稼働時間)
- 不適合品(廃棄品)の生産に要した材料(量と費用)
- クレーム等の調査・対策に要した工数(人工)
- 不適合品の回収に要した工数と費用(人工、運送費)
- 不適合品の選別に要する工数(人工)
- 不適合品の手直しに要した工数(人工)
- 不適合品の手直しに要した材料(量と費用)
- 代替品の生産に要した工数(人工)
- 代替品の生産に要した材料(量と費用)
6.2 分析・評価手法(QC7つ道具)
品質管理では、事実に基づいて、問題の状況を把握し、プロセス(工程)の良し悪しを判断し、PDCAを回しながら改善活動を行う。
品質管理に使われる手法(QC手法)は、統計的手法とも言われ、事実とデータを分析する。次に示す7つの手法が実際に多く使用されており、QC7つ道具と呼ばれている。
分析・評価を行う上で最も大切なことは、問題解決、又は課題達成のために、ツール(QC7つ道具)を活用してデータを収集・分析し、そこに示されている情報をしっかり読み取ることであり、得られた図や表から「何が言えるか」を考え、意見をまとめる。
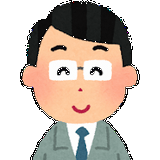
下表はQC7つ道具ですが、ISO9100ではISO9001に比べさらにレベルを上げる、または別の分析・評価手法を使うことになると考えています。
データの取得については、人が記録するのではなく自動で記録できるようにする工夫も必要になってきます。例えば、IoTを利用するにしても、プロセスと必要なデータについて創意工夫は必要です。
1 |
特性要因図 |
仕事の結果(特性)に対する原因(要因)を整理する。 ・品質特性に影響を与えている要因を探すのに役に立つ |
---|---|---|
2 |
管理図 |
工程が安定状態で維持管理されているか判断するための図 |
3 |
グラフ |
データの時間的変化や項目別の比較などを図的に見る。 ・データを一見して、誰にでもよく判るようにできる |
4 |
チェックシート |
チェックするだけで簡単に結果が分かる表や図 ・目的に合ったデータを簡単に取れ、確認の抜けも防止できる |
5 |
パレート図 |
問題点を見出し、重点指向(改善の優先順位)を可能にする。 ・最も重要な問題や原因を客観的に知ることができる。 |
6 |
ヒストグラム |
ばらつくデータの分布の特徴をつかむ。 ・取得したデータ(測定値)の全体の分布が見やすい。 |
7 |
散布図 |
対になった2種類のデータの関係を見つける。 ・「結果と原因」、「特性と特性」、「要因と要因」の関係を見る。 |
7. 製造工程の変更管理
7.1 製造工程変更時の注意点
製造又はサービス提供に関する変更は、必要な程度までレビューを行い管理する。
製造工程変更の管理には、以下のことを含める。
- 製造又はサービス提供の変更を承認する権限をもつ人々を明確にし、識別できるようにする。
- 製造又はサービス提供の変更には、工程、製造設備、治工具又はソフトウェアプログラムに影響を与える変更が含まれる場合がある。
- 変更のレビューの結果、変更を正式に許可した人(又は人々)及びレビューから生じた必要な処置を記載した、文書化した情報を保持する。
7.2 工程の変更
是正処置や顧客要求などにより、工程を変更する必要が生じた場合、製造部は工程変更に必要な情報(変更理由、製品名、変更内容、変更予定等)を明確にし、営業会議、開発会議において審議し、当該会議において承認を得る。
工程変更の承認後、工程変更に関連する部署は、必要な検証を行い、製品品質を確認した後、品質工程図等を改訂する。
工程変更の途中経過及び結果については、適宜当該会議等で報告する。
7.3 作業手順書、品質工程図の改定
製造部署は、工程変更の内容を検討し、必要に応じ「作業手順書」及び「品質工程図」を改訂する。
7.4 変化点管理(4M変更)
当社仕様による委託製造品(部品や加工・組立も含む)における4M変更については、「外注・購買管理規定(QM9100版)」を参照。
8. 識別及びトレーサビリティ
製品の識別およびトレーサビリティを容易にするため、材料・部品・製品の受入、製造及び引渡しまで「識別及びトレーサビリティ管理標準」に従い管理する。
製造部での製造における初工程から出荷まで次の通り管理する。
(1)製品識別として品名、ロット番号等を使用する。
(2)トレーサビリティを可能とするため、初工程から出荷まで製造ロット毎に個別に定めた識別で管理する。
(3)次工程において容易に識別出来る様に、製品識別を表示する。
(4)記録には、製品識別をはじめ、作業日、工程名、製品の基本性能に影響する材料、部品等のロット番号、作業条件、作業者等を記録する。
9. 顧客や外注・購買先から預かるもの(顧客支給品)の管理
本項に該当する例として、顧客から支給される材料がある。
9.1 顧客又は外部提供者の所有物の識別
(1)顧客からの支給品がある場合、その内容を営業部署が入手し、技術部に連絡する。
(2)技術部は内容を確認し図面等に反映させる。
(3)必要に応じ「品質工程図」に明記する。
9.2 顧客又は外部提供者の所有物の管理
(1)当該所有物は関係部署で、受入検査等を実施して異常のないことを確認し、保管する。
(2)当該所有物に不具合が発生した場合は、当該保管部署長は営業部及び顧客に報告し、処置について協議する。
9.3 顧客又は外部提供者の所有物の記録
(1)当該支給物品の員数等の記録は、所管部署で管理する。
(2)不具合発生時の処置、結果については、製造管理部署で必要な情報(支給先、対象製品名、支給数量、不適合数量、不適合内容、処理方法等)をまとめ、関連部署に連絡し、処理方法を決め、不適合品を処理する。
10. 製造工程の設計及び特殊工程の妥当性確認
10.1 製造工程の設計
(1)製造部署は、製作図面に基づき工程を設計し、品質工程図、作業手順書などを作成する。
(2)特殊工程についてはプロセスの妥当性確認を行う。
(3)製造準備段階での品質不良防止活動
量産開始までの製造準備を行う段階などにおいて、製品の品質に悪さをする(歩留を低下させる)要因をできる限り洗い出し(抽出し)、以下の事項を実施し事前に対策を行い不良の発生を防止する。
- 類似製品における過去のトラブル原因とその対策を確認し、生産準備を行う。
- 製造工程における「潜在的な悪さ」を洗い出し(摘出し)、未然に不良品発生の原因を取り除く。
特に次の3点を重要項目として実施する。
- 製造する製品の用途(どこに使われるか)を知る。
- 製品に対する顧客の品質要求事項(仕様)を把握する。
- 試作品(サンプル品)の評価をしっかり(確実に)実施する。
10.2 製造に関するプロセスの妥当性確認
(1)製品の製造工程において、事後の検査・試験等では検証が困難あるいは不可能な以下の特殊工程についての妥当性確認を行い、製造に関するプロセスが計画通りの結果をだせることを実証する。
特殊工程の例 溶接など
なお、「外注・購買管理規定(QM9100版)」で規定する委託加工の際も本項に準拠する。
特殊工程に従事する作業者は、「教育・訓練規定(QM9100版)」により認定する。
(2)次の事項について「製造に関するプロセスの妥当性確認基準」に定める。
- プロセスレビュー及び承認のための明確な基準
- 設備の承認及び要員の適格性確認
- 所定の方法及び手順の適用
- 妥当性の再確認
11. 試作管理
(1)試作の実施
試作品を製造部で製作する場合は、「設計・開発管理規程(QM9100版)」に基づき試作を実施する。
(2)試作関係の記録等の管理
試作関係の記録等は、「品質文書管理規程(QM9100版)」に従い管理する。
12. 記録の管理
製造に関する記録は、「品質文書管理規定(QM9100版)」により管理する。
【参考】製造に関する参考資料
製造に関する参考です。
- 製造管理について
- 工場などの安全衛生管理について
- モノづくりの品質について
- 作業手順書について
- RoHS関連
まとめ
ISO9100:2016版対応の「QM-9100版品質マニュアル」の関連規定の1つ、「製造管理規定(QM9100版)」の一例について説明しました。